Anti-corrosion Mechanism
Duplex coating is a combination of hot-dip galvanizing and epoxy coating. Firstly, product is hot-dip galvanized, and then epoxy powder is sprayed on the surface. The anchor bolt has better anti-corrosion performance and longer service life after two kinds of anti-corrosion processes. It can not only resist ordinary chemical corrosion, but also work in acidic environment and electrochemical corrosion with stray currents.
Product Standard
Duplex coating combines all the performance parameters of hot-dip galvanizing and epoxy coating. Hot-dip galvanizing meets the requirements of the table below. Epoxy products are mainly based on EN 13438 “Paints and varnishes - Powder organic coatings for hot dip galvanized or sherardized steel products for construction purposes”, with a minimum coating thickness of ≥60um. Bending performance of epoxy coating complies with ISO 1519 “Paints and varnishes - Bend test (cylindrical mandrel)”. Impact performance meets ASTM D2794 “Standard Test Method for Resistance of Organic Coatings to the Effects of Rapid Deformation (Impact)”. Adhesion conforms to ISO 2409 “Paints and varnishes -Cross-cut test”.
Product |
Mean Coating Thickness(min.)/μm |
Local Coating Thickness(min.)/μm |
Hollow Anchor Bar |
85 |
70 |
Coupler |
55 |
45 |
Nut |
55 |
45 |
Plate |
85 |
70 |
Centralizer |
55 |
45 |
Wedge |
55 |
45 |
Note: This table is for general use, and we can also meet customers' special requiretments. |
Technological Process
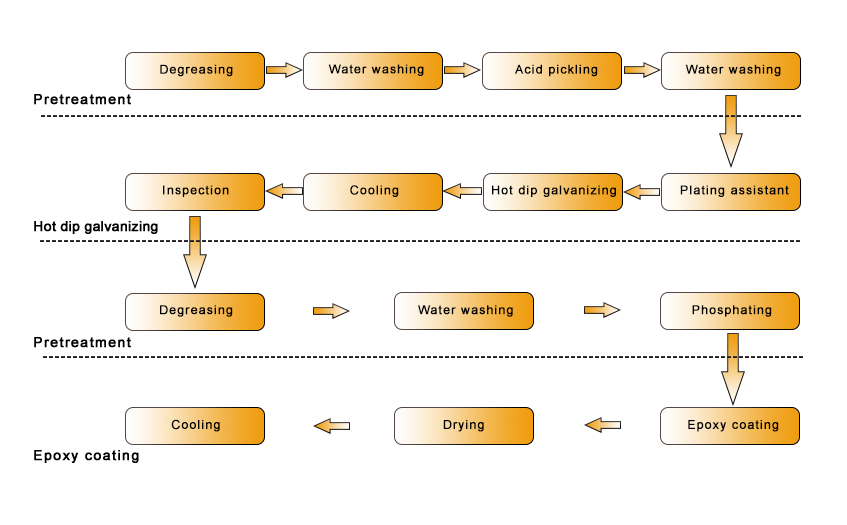
Featurs and Advantages
Excellent anti-corrosion properties: As zinc is an active metal, after coating surface is damaged, it will protect the steel by battery effect.
Long service life: Zinc layer is consumed very slowly in the atmosphere, so its service life far exceeds that of any other coatings.
Full protection: As immersed into hot-dip galvanizing bath,products are fully protected and anti-corrosion effect is better.
Lower price: In most cases, the hot-dip galvanizing cost is lower. Zinc coating is more durable than others, and does not require maintenance in the future.
High processing efficiency: Hot-dip galvanizing bath is simple and efficiency is higher than other coatings.
Not affect steel performance: Hot-dip galvanizing is carried out in an environment of more than 400 ℃, and will not affect the performance and toughness of steel.
The selected coating material is thermosetting, which has excellent chemical corrosion resistance, does not react with acids, alkalis, etc., makes the formed coating absolutely inert, completely prevents the anchor bolt from contacting with external environment and prevents corrosion.
After curing, the coating material will not melt even if it is heated again. It has high chemical stability. The formed coating has high adhesion to metal, low drying shrinkage and high ductility. In the case of the coating is not damaged during operation, it can effectively block corrosive substances.
Service Life
The service life of duplex coating anchor bolt is usually much longer than single anti-corrosion treatment, which is a synergistic effect. In most environments, the service life of duplex coating anchor bolt can reach 100 years without maintenance; the first maintenance service life of duplex coating anchor bolt in a severely corrosive environment is nearly double that of hot-dip galvanizing anchor bolt. Plesase see details in the table below.
Environments |
The years of first maintenance of hot-dip galvanizing anchor bolt
(85 um) |
The years of first maintenance of duplex coating anchor bolt |
C1: Interior, dry |
>200+ |
>200+ |
C2: Interior, condemnation,
Exterior, inland Country |
>170 |
>200+ |
C3: Interior, high humidity,
Exterior, inland city or mild coast |
42~170 |
>200+ |
C4: Interior, swimming pool,
Exterior, industrial area or coastal city |
21~ 42 |
42~ 84 |
C5: Exterior, industrial area with high humidity and coastal area with high salinity |
10~ 21 |
18~ 37 |
Application
Duplex coating anchor bolt is generally used in the permanent support of hydro-projects, underwater tunnels, subway tunnels and some important buildings affected by groundwater for a long time. And it is also widely used in harbors, wharfs, offshore buildings which are corroded by seawater.