Why Using Self-drilling Hollow Bolt As Anti-floating Rock Anchor Pile?
Time:2024-10-12From:sinorock View:
As an advanced method of foundation supporting, self-drilling hollow bolt is widely used as civil construction foundation, tower foundation, soundproof wall foundation, new building pile foundation, and anti-floating rock anchor pile. It’s easy to understand that using self-drilling hollow bolt as the foundation of different constructions. However, why using it as anti-floating rock anchor pile? And how?
What Is Self-drilling Hollow Bolt?
It is a rock anchoring system that contains a one-time use drill bit, a rock bolt with an inner hole, a coupler to double, or triple the hollow bolt or even, a combination of a plate and a nut to transform the load to hollow bolt, and a centralizer to ensure the hollow bolt staying at the central of the drilling hole.
The designation of inner hole of the rock bar makes it possible to drill and grout simultaneously. Therefore, it is suitable for unstable geological conditions where are difficult to drill holes or the drilling hole collapse easily, such as broken rock, loose soil, and others.
Construction Process of Using Self-drilling Hollow Bolt As Anti-floating Rock Anchor Pile
Preparation before construction: Check whether the functions of the drilling rig are normal, whether the drill bit and the rod body are damaged, and whether the inner path of rod body is unblocked, etc. After all these preparation is OK, screw to connect the hollow bolt body to be used with the drill bit;
Drill and grouting: Connect the rod body and the grouting tube to the drilling rig through a rotary grouting adapter, and grouting during the drilling process to achieve simultaneous completion of drilling and grouting;
Extend the length of hollow bolt: If the length of a single self-drilling anchor bolt cannot reach the designed drilling depth, the couplers can be used to double or triple the hollow bolt to meet the design requirements;
Install the backing plate and nut: After the grouting is completed, install the backing plate and the nut in sequence on the exposed part of the self-drilling anchor bolt outside the rock body close to the construction surface to ensure the anchoring effect.
Anti-Floating Rock Anchor Pile Specification (one of all)
.jpg)
Hollow Bar
Size | Outer Dia. (mm) |
Ultimate Load (kN) |
Yield Load (kN) |
Weight (Kg/m) |
SER25N | 25 | 200 | 150 | 2.35 |
.jpg)
Coupler
Size | Outer Dia. (mm) |
Length (mm) |
Weight (Kg/pc) |
Note |
SSR25 | 36 | 150 | 0.66 | With sealing structure |
SER25 | 36 | 150 | 0.68 | Without sealing structure |
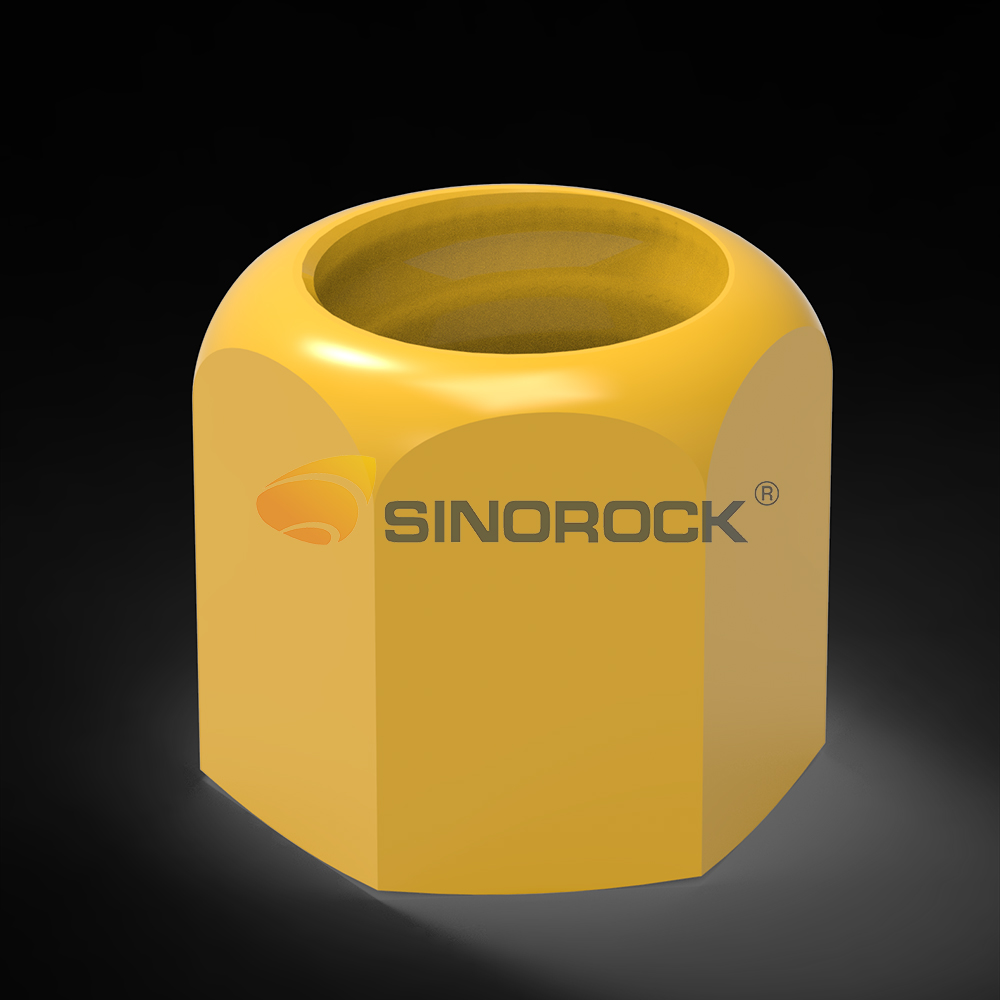
Hex Nut
Size | Key Size (mm) |
Length (mm) |
Weight (Kg/pc) |
Note |
SSR25 | 41 | 30 | 0.20 | Heat treatment |
SER25 | 41 | 35 | 0.23 | Without heat treatment |
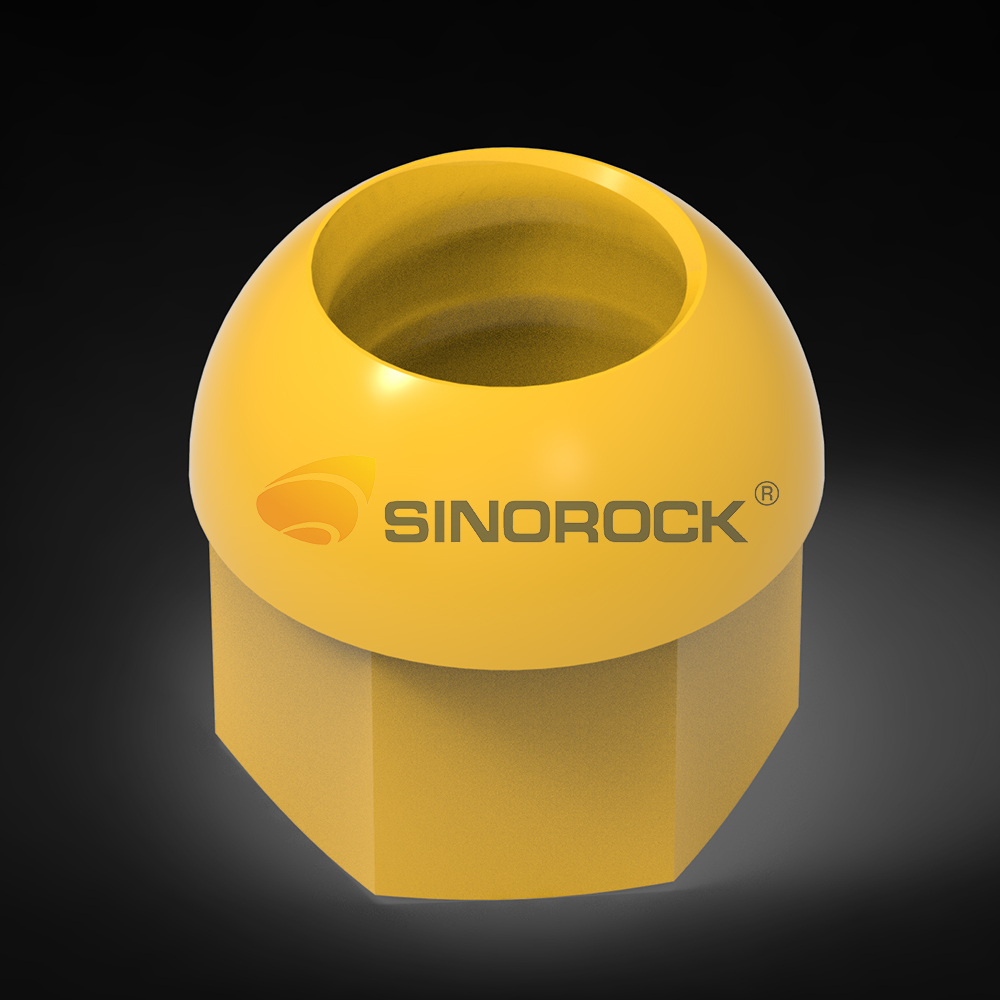
Domed Nut
Size | Key Size (mm) |
Length (mm) |
Weight (Kg/pc) |
Note |
SER25 | 41 | 40.5 | 0.31 | Without heat treatment |
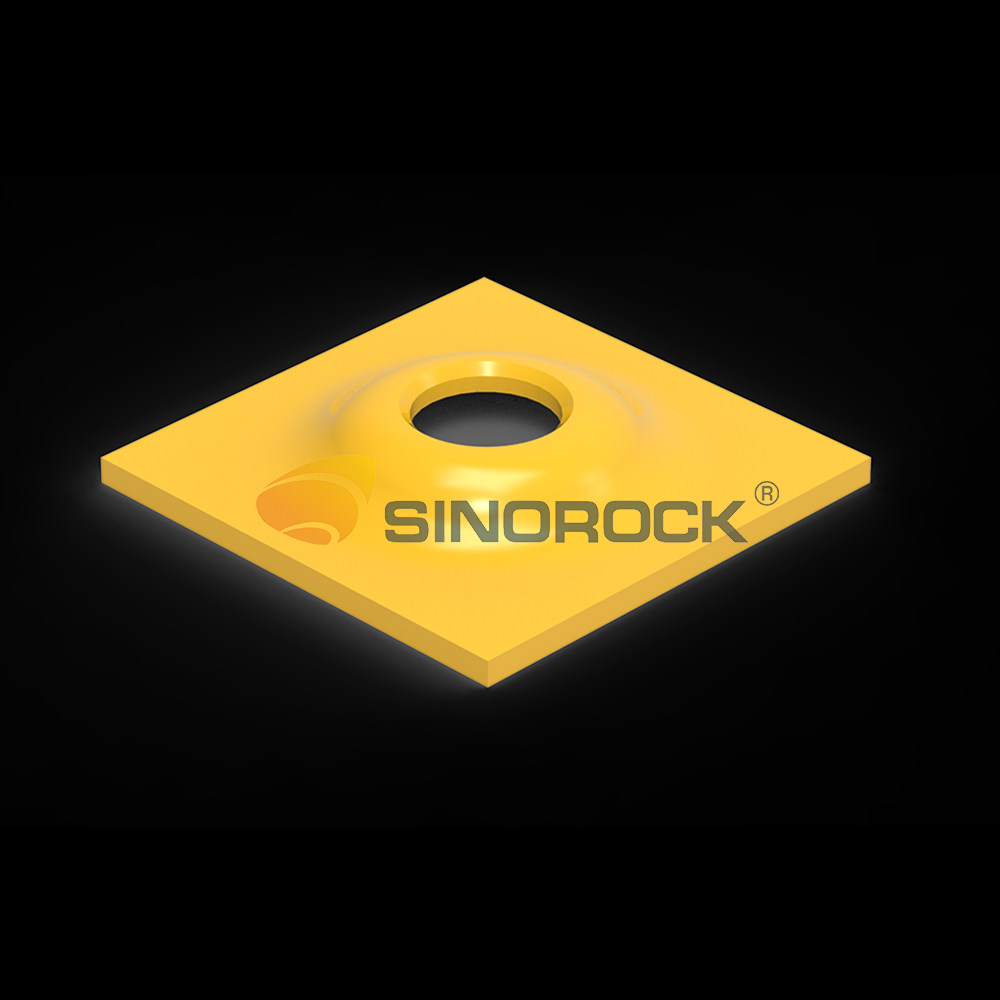
Domed Plate
Size | Dimensions (mm) |
Thickness (mm) |
Hole Dia. (mm) |
Weight (Kg/pc) |
SER25 | 150×150 | 8 | 30 | 1.40 |
150×150 | 5 | 28 | 0.85 | |
200×200 | 10 | 32 | 3.20 |
.jpg)
.jpg)
.jpg)
.jpg)
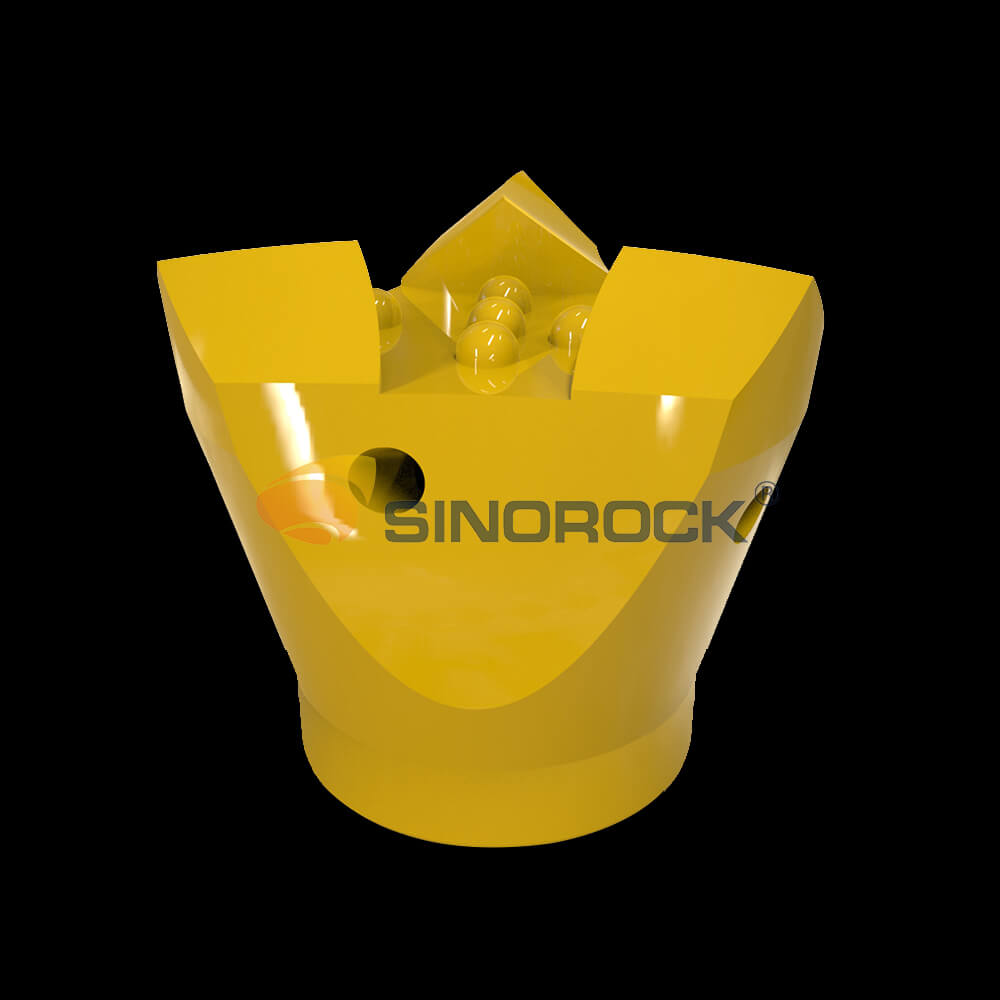
Drill Bit
Size | Outer Dia. | Application Range (Advice) | ||
(mm) | ||||
EX | Sand, fills, gravel | |||
SSR25/42 | 42 | |||
SSR25/51 | 51 | |||
EXX | Softer sedimentary rocks such as marls, mudstones, siltstone | |||
SSR25/42 | 42 | |||
SSR25/51 | 51 | |||
ES-F | Gravel, soft rock | |||
SSR25/42 | 42 | |||
SSR25/51 | 57.5 | |||
ESS-F | Weathered rock, stone walls, rubble | |||
SSR25/42 | 42 | |||
SSR25/51 | 51 | |||
EY | Competent ground, strong rock | |||
SSR25/51 | 51 |
Why Using Self-drilling Hollow Bolt As Anti-floating Rock Anchor Pile?
In modern construction engineering, anchoring systems play a critical role in maintaining stability and preventing structural failures. One common issue in foundation design is the uplift or floating effect that occurs due to groundwater pressure or buoyant forces. To counteract this, rock anchor piles are used, and increasingly, the self-drilling hollow bolt has become a preferred solution as an anti-floating rock anchor pile. This article will explore why self-drilling hollow bolts are highly effective in this application, focusing on their performance, durability, ease of installation, and the current state of the industry.
The Importance of Anti-floating Measures in Construction
In many construction projects, especially those located in areas with high groundwater levels or frequent rainfall, the foundations are exposed to uplift pressure. When the buoyant force from underground water exceeds the weight of the structure, the foundation may begin to lift, leading to significant structural instability. This phenomenon is known as floating or uplift.
Anti-floating measures, such as the installation of rock anchor piles, are necessary to stabilize the structure and ensure safety. Traditional anchor piles, such as rebar anchors, are often used for this purpose. However, as construction techniques evolve, more advanced materials and systems, like the self-drilling hollow bolt, have proven to offer superior performance.
Self-drilling Hollow Bolt: A Modern Solution for Anti-floating Rock Anchoring
Self-drilling hollow bolts have gained recognition in the construction industry due to their versatility and efficiency. They are particularly effective in anti-floating applications for several reasons, including their corrosion resistance, installation efficiency, and material strength.
Corrosion Resistance for Challenging Environments
One of the major advantages of using self-drilling hollow bolts as anti-floating rock anchor piles is their ability to withstand harsh environmental conditions. Many construction projects are located in coastal areas, wetlands, or other regions where the foundations are continuously exposed to moisture, saltwater, and corrosive elements. Under these conditions, traditional rebar is highly susceptible to corrosion, which can lead to reduced performance and eventual structural failure.
Self-drilling hollow bolts, when made from corrosion-resistant materials such as stainless steel, hot-dip galvanized steel, or epoxy-coated steel, offer excellent protection against these environmental challenges. Stainless steel is particularly known for its resistance to rust and chemical degradation, making it an ideal choice for projects near coastal areas or where groundwater is a concern.
For instance, in coastal construction projects or in areas with high groundwater levels, the risk of corrosion is amplified due to the constant exposure to moisture and salts. Unlike rebar, which would degrade quickly in such conditions, self-drilling hollow bolts maintain their integrity, ensuring the long-term stability of the foundation.
Grouting During Drilling: Improved Construction Efficiency
Another key advantage of self-drilling hollow bolts is their ability to integrate the grouting process with the drilling process. Traditional rock anchor piles often require a separate step for grouting after the anchor has been installed, which adds time and complexity to the construction process. However, with self-drilling hollow bolts, grouting can be completed simultaneously with the drilling operation.
This dual-functionality not only streamlines the installation process but also enhances the bond between the bolt and the surrounding rock or soil. The grout is injected directly through the hollow core of the bolt, filling any voids or cracks within the drilled hole and ensuring that the bolt is securely anchored. This method is particularly advantageous in unstable or loose ground conditions where achieving proper anchoring is crucial.
By reducing the number of construction steps and improving installation efficiency, self-drilling hollow bolts save time and labor costs, making them an attractive option for large-scale projects.
Material Strength and Wear Resistance
In addition to their corrosion resistance and installation efficiency, self-drilling hollow bolts are known for their high strength and wear resistance. These bolts are often made from materials like stainless steel, which offers excellent mechanical properties, including tensile strength and weldability.
The strength of these bolts ensures that they can withstand significant loads and stresses, which is essential for anti-floating applications. When used as rock anchor piles, self-drilling hollow bolts provide the necessary resistance to uplift forces caused by groundwater pressure, ensuring the stability of the structure.
Wear resistance is another important factor, particularly in environments where the bolts may be exposed to abrasive materials or heavy loads. The durability of self-drilling hollow bolts makes them suitable for long-term use in challenging conditions, reducing the need for frequent maintenance or replacement.
Applications in Anti-floating Foundation Projects
Given their performance advantages, self-drilling hollow bolts are widely used in various types of anti-floating foundation projects. These projects can include underground structures like basements, tunnels, and underground parking garages, as well as bridges, dams, and coastal infrastructure.
In anti-floating applications, the self-drilling hollow bolt acts as a rock anchor pile that provides vertical restraint, counteracting the buoyant forces exerted on the foundation. By anchoring the structure to the underlying rock or soil, these bolts prevent upward movement, ensuring the stability and safety of the construction.
Moreover, self-drilling hollow bolts are not limited to anti-floating applications. They are also used in slope stabilization, foundation support, and tunnel reinforcement, making them a versatile solution for a wide range of geotechnical challenges.
The Role of Sinorock in the Industry
Sinorock, a leading manufacturer of geotechnical engineering solutions, provides a comprehensive range of self-drilling hollow bolts that are specifically designed for anti-floating and other anchoring applications. Sinorock’s self-drilling hollow bolts are manufactured to meet the highest industry standards, ensuring superior performance in corrosive environments and challenging ground conditions.
With a focus on quality and innovation, Sinorock has established itself as a trusted provider of anchoring solutions for construction projects around the world. The company offers a variety of bolt sizes, materials, and configurations to meet the specific needs of each project, ensuring that engineers have the right tools to achieve optimal results.
Conclusion
Self-drilling hollow bolts have revolutionized the way anti-floating measures are implemented in construction projects. Their corrosion resistance, grouting efficiency, material strength, and versatility make them a superior choice for rock anchor piles in challenging environments. As the construction industry continues to evolve, the demand for reliable and efficient anchoring systems will only increase, and self-drilling hollow bolts are well-positioned to meet this demand.
For any construction project facing uplift pressure or challenging ground conditions, using self-drilling hollow bolts as anti-floating rock anchor piles offers a reliable and long-lasting solution. Sinorock, with its extensive expertise and high-quality products, is at the forefront of providing these essential anchoring systems to the industry.
latest news
-
- 3 Crucial Factors That Impact the Quality of Self-Drilling Hollow Bolts
- Time:2025-01-26From:This Site
- As we all know, the quality of the self-drilling hollow bolts is vital to the whole project. It determines if the project is safe for the people in future use. Then, what will affect the quality of the self-drilling hollow bolts?
- View details
-
- Self-Drilling Anchor Bolt Construction in Complex Geological Slope
- Time:2025-01-24From:This Site
- During construction, Self-drilling hollow anchor bolt integrates drilling, grouting and anchoring functions, which significantly improves drilling efficiency. And under the action of pressure pump, the grouting in the rock strata and voids is full, which ensures the grouting thickness and anchoring effect.
- View details
-
- How Does Self-drilling Rock Bolt Drill in Quicksand Geological Condition?
- Time:2025-01-19From:This Site
- This in-depth guide explores how self-drilling rock bolts function in quicksand geological conditions, covering the challenges, construction methods, and best practices for ensuring effective anchorage in unstable, fluidic soil layers.
- View details
-
- Quality Control: the Vital Factor of A SDA Bolt Factory
- Time:2025-01-09From:This Site
- Sinorock’s comprehensive quality control system, from supplier management to outgoing inspections, ensuring the highest standards for self-drilling anchor bolts in construction.
- View details
-
- International Women's Day with Strawberry-picking
- Time:2024-03-09From:This Site
- Marked the annual observance of International Women's Day, and to commemorate this significant event, Sinorock organized a special strawberry-picking event exclusively for its female employees.
- View details
-
- Celebrate the 74th anniversary of the founding of the People's Republic of China
- Time:2023-10-01From:This Site
- On October 1st every year, we observe the annual National Day, commemorating the birth of our beloved motherland.
- View details
-
- SINOROCK to Attend EXPOMINA PERÚ 2024 in Lima, Peru
- Time:2024-08-10From:This Site
- Sinorock to Attend EXPOMINA PERÚ 2024 in Lima, Peru
- View details
-
- SINOROCK to Participate in MINING AND METALS CENTRAL ASIA 2024
- Time:2024-08-08From:This Site
- SINOROCK to Participate in MINING AND METALS CENTRAL ASIA 2024
- View details
-
- SINOROCK Gears Up for UGOL ROSSII & MINING 2024 with Custom Mining Solutions
- Time:2024-05-15From:This Site
- SINOROCK is thrilled to announce its participation in the highly anticipated 32nd International Trade Fair for Mining Technology, UGOL ROSSII & MINING 2024. The event will take place at the Exhibition complex "Kuzbass Fair" in Novokuznetsk, Kemerovo region - Kuzbass, Russia, from June 4th to 7th, 2024.
- View details