Things About Rock Bolt You Need to Know
Time:2023-12-15From:sinorock View:
Introduction to Rock Bolts
In the intricate world of geotechnical engineering, the humble rock bolt emerges as a stalwart, fortifying loose, fractured, and unstable soil and rock formations. This critical support system plays a pivotal role in ensuring the stability of excavations, making it an indispensable component in construction projects.
Types of Rock Bolts
1. Grout-Anchored Rock Bolt
The grouted rock bolt, a threaded steel or rebar structure, stands as a testament to versatility. Cement grout or resin grout is employed as the grouting agent, enhancing reinforcement. A cable bolt, resembling a steel rope, intertwines with the grout in the borehole, ensuring robust stability. This type finds application in a spectrum of excavation scenarios.
2. Cable Bolts
Ideal for temporary or permanent rock reinforcement, cable bolts eschew tensioners for a more flexible system. With options for cement cartridges, resin cartridges, or injection resin, cable bolts shine in conditions with space constraints, excelling in roadway and gateway reinforcement.
3. Hollow Rock Bolts
Featuring a central hole for grout, hollow rock bolts simplify the grouting process. With a mechanism akin to cone and wedge anchors, these bolts adapt to diverse orientations, making them a reliable choice for challenging terrains.
4. Mechanically Anchored Rock Bolts
Employing an expansion shell instead of grout, mechanically anchored rock bolts distribute load evenly along the rock face. The wedge attached to the bolt shank adopts a conical shape upon rotation, ensuring friction and interlock for enhanced reinforcement.
5. Friction-Anchored Rock Bolts
The friction-anchored rock bolt introduces radial force against the borehole wall, creating frictional resistance. A recent innovation, this bolt technique minimizes sliding post-installation, adding a layer of security to the support system.
6. MDX Bolt
Designed for seismic rock conditions, the MDX bolt surpasses expectations in ground support stability. With a unique wedge enabling significant expansion without the need for grout or resin, these bolts provide a solid anchor in squeezing ground, mitigating seismic risks.
7. Fiber-Reinforced Polymer Composite Rock Bolts
In environments hostile to steel bolts, such as coal mines with rapid corrosion, FRP rock bolts shine. Their corrosion resistance, non-conductive nature, and ease of installation make them a preferred choice in harsh conditions.
8. Dowel
A dowel, an untensioned steel rod, activates upon ground displacement. Ideal for joints subject to displacement, dowels withstand both shear and tensile stresses, offering a tailored solution based on grout material and ground support requirements.
9. Self-Drilling Rock Bolt
A revolutionary solution combining drilling, grouting, and anchoring, the self-drilling rock bolt streamlines the installation process. Available in R thread and T thread varieties, these bolts cater to various geological demands.
With diameters ranging from 25mm to 200mm, self-drilling rock bolts come in stainless steel, hot dip galvanizing, epoxy coating, and duplex coating variants. Each variant is tailored to specific geotechnical engineering applications, ensuring optimal performance.
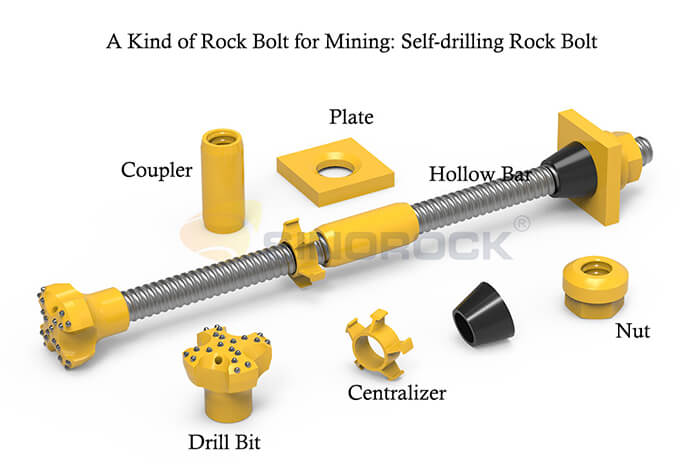
The Reinforcements Used With Rock Bolts
1. Sprayed Concrete
Applied post-rock bolt installation, sprayed concrete, in gunite or shotcrete forms, accelerates stabilization. Shotcrete, with a lower rebound rate, proves more efficient, while fibers can be added for increased strength.
2. Lattice Girders
Triangular steel frames, known as lattice girders, offer immediate support and complement shotcrete applications. These lightweight structures, when combined with strata bolts, enhance forward support.
3. I Beam Girders
Heavy steel frames spanning tunnel widths, I beam girders offer robust support in weak rock formations. However, their shape can degrade shotcrete quality, necessitating careful consideration in application.
Construction Process of Rock Bolts
The construction process of rock bolts, exemplified by self-drilling rock bolts, involves a meticulous step-by-step process. From drilling and grouting to tensioning, this video demonstration showcases the intricacies of ensuring a robust rock support system.
Factors Affecting Rock Bolt Performance
Ensuring the optimal performance of rock bolts is contingent upon a nuanced understanding of the myriad factors that influence their effectiveness and longevity. Key variables come into play, with rock type, bolt length, and grout quality emerging as pivotal determinants. The nature of the rock itself plays a significant role, as different geological formations may necessitate tailored approaches. Moreover, the length of the bolt and the quality of the grouting material are critical considerations, directly impacting the bolt's ability to provide enduring stability. Precision in addressing these factors is paramount, underscoring the importance of meticulous planning and execution in rock bolt installations. As the backbone of geotechnical support, rock bolts demand a comprehensive comprehension of these influencing elements to ensure their reliable performance in diverse construction scenarios.
Fields of Applications of Rock Bolt
Rock bolts find application in diverse geotechnical domains:
1. Tunnel and Underground Engineering
Critical for initial tunnel support, rock bolts aid in high-pressure grouting, fortifying soil and rock masses to ensure surface stability. Various types of support, including fore-piling, radial support, and tunnel-face support, underscore their versatility.
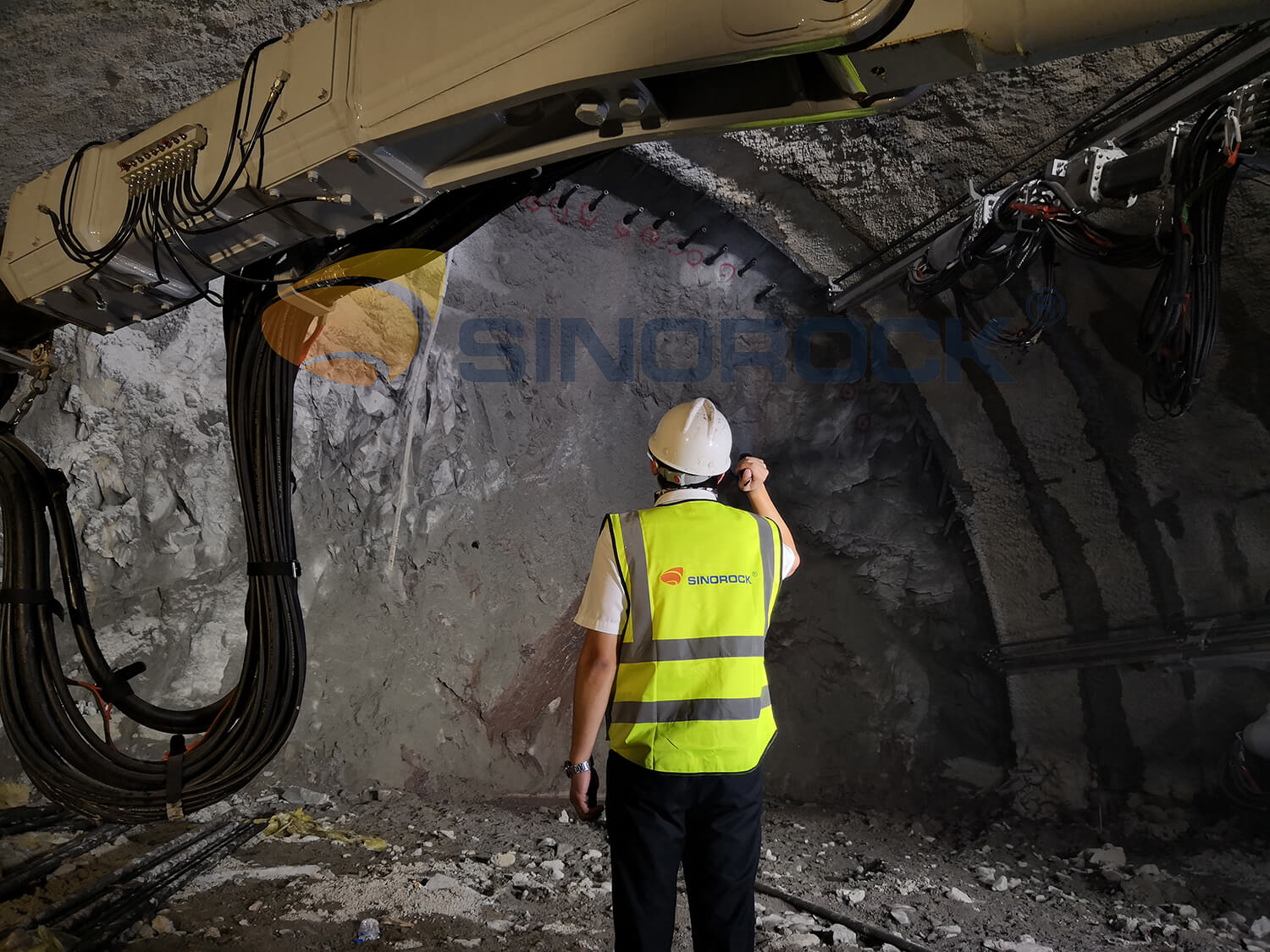
2. Slope Stabilization Project
Addressing challenging geological environments, rock bolts play a pivotal role in slope stabilization. Offering solutions like soil nail support, slope protection barriers, and retaining walls, they become a linchpin in diverse scenarios.
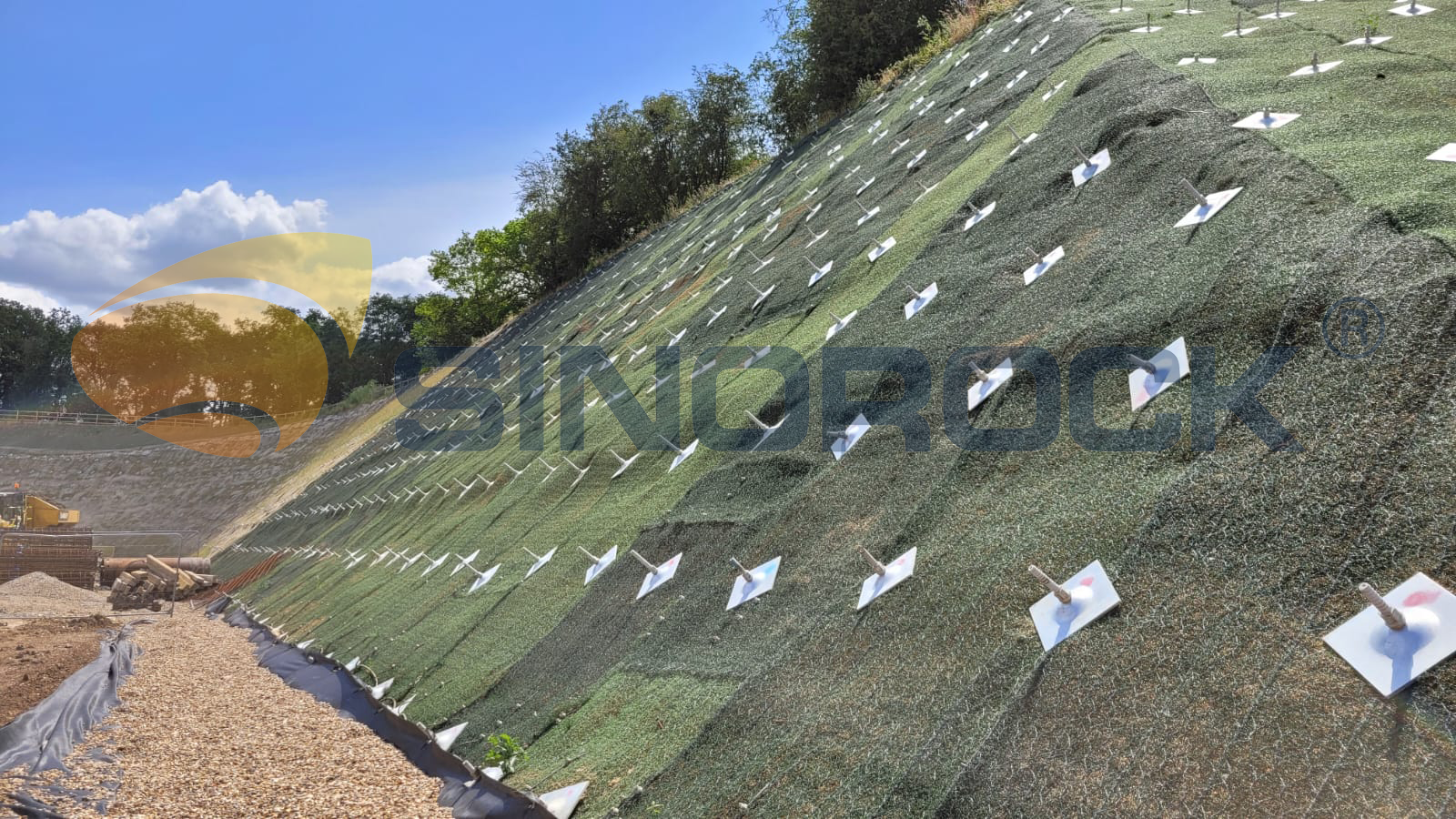
3. Ground and Foundation Project
In micropile applications, rock bolts facilitate the transfer of pressure, tension, or periodic loads to the surrounding soil. This versatile application extends to new building pile foundations, structural repairs, and various other scenarios demanding robust ground support.
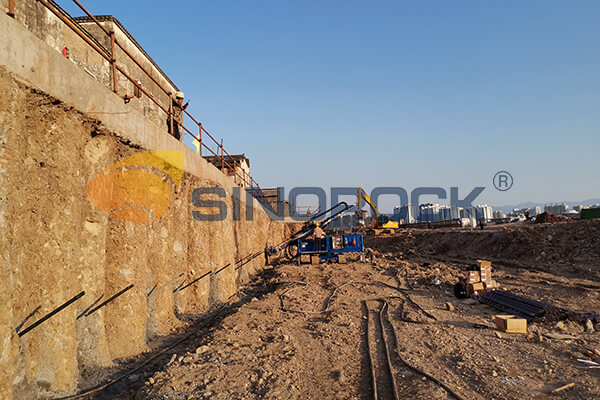
Safety Considerations
1. Training Protocols
Rigorous training programs are indispensable. Ensuring all personnel involved in rock bolt installations are well-versed in safety protocols is foundational. From understanding potential hazards to mastering installation procedures, comprehensive training reduces the risk of accidents.
2. Regular Inspections
Scheduled inspections form a cornerstone of safety measures. By routinely examining rock bolt installations, any potential issues or weaknesses can be identified and rectified promptly. This proactive approach mitigates risks and contributes to the overall reliability of the support system.
3. Maintenance Practices
Meticulous maintenance practices play a pivotal role in sustaining rock bolt efficacy. Regular checks and upkeep prevent deterioration, ensuring that the installed rock bolts remain in optimal condition throughout their operational lifespan. This preventive strategy enhances safety and promotes long-term stability.
4. Adherence to Protocols
Strict adherence to established safety protocols during the installation process is imperative. Whether it involves drilling, grouting, or tensioning, following industry-standard procedures minimizes the likelihood of accidents and ensures a secure working environment.
5. Emergency Preparedness
Being prepared for unforeseen circumstances is integral. Establishing clear emergency protocols, including evacuation procedures and first aid measures, enhances the overall safety net and safeguards against potential risks associated with rock bolt applications.
6. Continuous Training and Updates
Given the evolving nature of construction practices, continuous training and updates are essential. Staying abreast of the latest safety standards and technologies ensures that the workforce remains equipped to handle any challenges that may arise in the dynamic field of rock bolt applications.
Conclusion
Rock bolts, a fundamental component of geotechnical engineering, are silent guardians that fortify the foundation of ambitious construction projects. The diverse types of rock bolts can be used for numerous applications, including in tunnels, slopes, and foundations. The immense impact they have on construction safety is undeniable, as they not only provide a stable foundation but also ensure the overall safety of the structure. The installation process can be complex, and proper attention must be paid to safety to ensure the longevity of the structure.
Sinorock has a professional product research and development team that makes customized services available. Sinorock aims to become a famous brand globally in the geotechnical industry and provides a one-stop solution for anchoring products for customers all over the world. If you have any needs or questions in the field of geotechnical anchoring, please feel free to contact us at sinorock@sinorockco.com.
latest news
-
- 3 Crucial Factors That Impact the Quality of Self-Drilling Hollow Bolts
- Time:2025-01-26From:This Site
- As we all know, the quality of the self-drilling hollow bolts is vital to the whole project. It determines if the project is safe for the people in future use. Then, what will affect the quality of the self-drilling hollow bolts?
- View details
-
- Self-Drilling Anchor Bolt Construction in Complex Geological Slope
- Time:2025-01-24From:This Site
- During construction, Self-drilling hollow anchor bolt integrates drilling, grouting and anchoring functions, which significantly improves drilling efficiency. And under the action of pressure pump, the grouting in the rock strata and voids is full, which ensures the grouting thickness and anchoring effect.
- View details
-
- How Does Self-drilling Rock Bolt Drill in Quicksand Geological Condition?
- Time:2025-01-19From:This Site
- This in-depth guide explores how self-drilling rock bolts function in quicksand geological conditions, covering the challenges, construction methods, and best practices for ensuring effective anchorage in unstable, fluidic soil layers.
- View details
-
- Quality Control: the Vital Factor of A SDA Bolt Factory
- Time:2025-01-09From:This Site
- Sinorock’s comprehensive quality control system, from supplier management to outgoing inspections, ensuring the highest standards for self-drilling anchor bolts in construction.
- View details
-
- International Women's Day with Strawberry-picking
- Time:2024-03-09From:This Site
- Marked the annual observance of International Women's Day, and to commemorate this significant event, Sinorock organized a special strawberry-picking event exclusively for its female employees.
- View details
-
- Celebrate the 74th anniversary of the founding of the People's Republic of China
- Time:2023-10-01From:This Site
- On October 1st every year, we observe the annual National Day, commemorating the birth of our beloved motherland.
- View details
-
- SINOROCK to Attend EXPOMINA PERÚ 2024 in Lima, Peru
- Time:2024-08-10From:This Site
- Sinorock to Attend EXPOMINA PERÚ 2024 in Lima, Peru
- View details
-
- SINOROCK to Participate in MINING AND METALS CENTRAL ASIA 2024
- Time:2024-08-08From:This Site
- SINOROCK to Participate in MINING AND METALS CENTRAL ASIA 2024
- View details
-
- SINOROCK Gears Up for UGOL ROSSII & MINING 2024 with Custom Mining Solutions
- Time:2024-05-15From:This Site
- SINOROCK is thrilled to announce its participation in the highly anticipated 32nd International Trade Fair for Mining Technology, UGOL ROSSII & MINING 2024. The event will take place at the Exhibition complex "Kuzbass Fair" in Novokuznetsk, Kemerovo region - Kuzbass, Russia, from June 4th to 7th, 2024.
- View details