The Design of Self Drilling Anchor Bolt
Time:2025-02-07From:sinorock View:
1. Introduction
One such innovation is the self-drilling anchor (SDA) system, which has revolutionized the construction and mining industries. This advanced anchoring technology eliminates the need for pre-drilling, allowing simultaneous drilling, grouting, and anchoring, making it particularly effective in complex geological environments.
This article delves into the design principles, key components, testing methods, and real-world applications of self-drilling anchor bolts while exploring future advancements in their technology.
2. Evolution of Self-Drilling Anchor Systems
Traditional anchor bolts require separate drilling, casing, and grouting processes, making installation cumbersome, time-consuming, and expensive. These challenges led to the development of self-drilling anchor bolts, which integrate drilling and anchoring into a single step.
Comparison with Conventional Anchors
Feature | Conventional Anchor Bolts | Self-Drilling Anchor Bolts |
Drilling Method | Requires pre-drilling and casing | Self-drills without casing |
Installation Time | Time-consuming | Faster and more efficient |
Performance in Loose Ground | Limited | Excellent |
Grouting Process | Separate grouting needed | Simultaneous grouting |
By eliminating casing and pre-drilling, SDA bolts have become indispensable for construction in unstable, water-bearing, or fractured geological formations.
3. Engineering and Design Principles of Self-Drilling Anchor Bolts
Key Components and Their Functions
1. Hollow Anchor Bar – The main load-bearing component, allowing grout injection for enhanced bonding.
2. Drill Bit – Facilitates drilling in various soil and rock conditions.
3. Coupling – Connects multiple anchor bars for deeper installations.
4. Nut and Plate – Transfers loads and ensures structural stability.
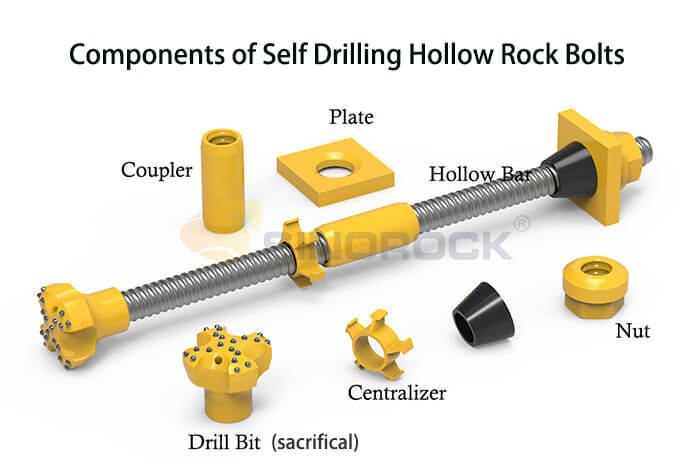
Material Selection
• High-strength steel for durability and load-bearing capacity.
• Corrosion-resistant coatings (zinc-plating, hot-dip galvanization) for extended lifespan.
Thread Profile
• Continuous threading along the bar ensures strong adhesion with grout.
• Optimized thread design enhances bonding and load transfer.
4. Grouting Mechanism and Bonding Strength
Grouting is a crucial element in SDA system performance, serving the dual purpose of:
1. Bonding the anchor bolt with surrounding ground.
2. Protecting against corrosion and enhancing long-term stability.
Factors Affecting Grouting Efficiency
• Grout Material: Cement-based grouts provide excellent adhesion.
• Injection Pressure: Higher pressures ensure deeper penetration.
• Soil/Rock Condition: Affects grout flow and final bonding strength.
Grouting significantly increases the shear and tensile strength of the anchorage system, making it effective in weak or water-logged formations.
5. Performance Testing and Design Validation
Pulling Test for Anchorage Strength
To validate the SDA system’s performance, a pull-out test is conducted, which measures:
• Bonding strength between grout and soil.
• Ultimate load capacity before failure.
Load-Bearing Analysis
• Determines optimal bolt length, diameter, and spacing.
• Analyzes soil conditions to ensure reliable support.
These tests ensure safe and effective application in real-world geotechnical conditions.
6. Practical Design Considerations in Geotechnical Engineering
SDA bolts are tailored for specific construction needs, considering:
• Load requirements (anchorage force and depth).
• Spacing and array layout for maximum efficiency.
• Site-specific geological conditions.
For example, in tunnel construction, SDA bolts provide rapid reinforcement, reducing excavation risks and improving stability.
7. Applications of Self-Drilling Anchor Bolts
SDA bolts are widely used in various geotechnical engineering fields, including:
• Slope stabilization: Preventing landslides in loose soil.
• Tunnel support: Reinforcing underground structures.
• Foundation reinforcement: Strengthening weak ground conditions.
• Mining and underground excavations: Providing structural stability.
• High water-bearing strata: Preventing collapses in water-logged areas.
These applications highlight the versatility and reliability of self-drilling anchor systems.
8. Conclusion
Self-drilling anchor bolts have transformed modern construction, offering efficient, reliable, and cost-effective solutions for challenging ground conditions. Their innovative design, ease of installation, and adaptability make them a cornerstone of geotechnical engineering.
As materials, designs, and technologies evolve, SDA bolts will continue to shape the future of construction, tunneling, and mining, reinforcing structures and ensuring long-term stability across diverse geological landscapes.
latest news
-
- The Design of Self Drilling Anchor Bolt
- Time:2025-02-07From:This Site
- Self drilling anchor bolt is a hollow, thick-walled seamless steel pipe, with standard continuous thread on its surface. Discover the design, components, and applications of self-drilling anchor bolts, ensuring stability in geotechnical engineering.
- View details
-
- 3 Crucial Factors That Impact the Quality of Self-Drilling Hollow Bolts
- Time:2025-01-26From:This Site
- As we all know, the quality of the self-drilling hollow bolts is vital to the whole project. It determines if the project is safe for the people in future use. Then, what will affect the quality of the self-drilling hollow bolts?
- View details
-
- Self-Drilling Anchor Bolt Construction in Complex Geological Slope
- Time:2025-01-24From:This Site
- During construction, Self-drilling hollow anchor bolt integrates drilling, grouting and anchoring functions, which significantly improves drilling efficiency. And under the action of pressure pump, the grouting in the rock strata and voids is full, which ensures the grouting thickness and anchoring effect.
- View details
-
- Quality Control: the Vital Factor of A SDA Bolt Factory
- Time:2025-01-09From:This Site
- Sinorock’s comprehensive quality control system, from supplier management to outgoing inspections, ensuring the highest standards for self-drilling anchor bolts in construction.
- View details
-
- International Women's Day with Strawberry-picking
- Time:2024-03-09From:This Site
- Marked the annual observance of International Women's Day, and to commemorate this significant event, Sinorock organized a special strawberry-picking event exclusively for its female employees.
- View details
-
- Celebrate the 74th anniversary of the founding of the People's Republic of China
- Time:2023-10-01From:This Site
- On October 1st every year, we observe the annual National Day, commemorating the birth of our beloved motherland.
- View details
-
- SINOROCK to Attend EXPOMINA PERÚ 2024 in Lima, Peru
- Time:2024-08-10From:This Site
- Sinorock to Attend EXPOMINA PERÚ 2024 in Lima, Peru
- View details
-
- SINOROCK to Participate in MINING AND METALS CENTRAL ASIA 2024
- Time:2024-08-08From:This Site
- SINOROCK to Participate in MINING AND METALS CENTRAL ASIA 2024
- View details
-
- SINOROCK Gears Up for UGOL ROSSII & MINING 2024 with Custom Mining Solutions
- Time:2024-05-15From:This Site
- SINOROCK is thrilled to announce its participation in the highly anticipated 32nd International Trade Fair for Mining Technology, UGOL ROSSII & MINING 2024. The event will take place at the Exhibition complex "Kuzbass Fair" in Novokuznetsk, Kemerovo region - Kuzbass, Russia, from June 4th to 7th, 2024.
- View details