3 Featured Characters of Self Drilling Rock Anchor Systems
Time:2023-07-20From:sinorock View:
Rock anchoring plays a crucial role in various industries such as construction, mining, and infrastructure development. As the demand for reliable and efficient anchoring solutions continues to grow, self-drilling anchor systems have emerged as a game-changer. With a range of unique features, these systems offer a reliable and efficient solution for securing unstable slopes, foundations and underground constructions. One of the key factors contributing to the success of these systems is the use of featured characters that enhance their performance and durability. In this article, we will explore three of the most prominent featured characters of self-drilling anchor systems..png)
Self-Drilling Capability
The first and foremost featured character of self-drilling anchor systems is their ability to drill into the ground without the need for pre-drilling. Traditional anchoring methods require pre-drilling of boreholes before the installation of the anchors. This time-consuming process often results in increased labor costs and extended project timelines. However, self-drilling anchor systems eliminate this step by connecting a drill bit at the leading end of the anchor bar. They feature a hollow threaded bar with a drill bit attached at the leading end. As the anchor bar is advanced into the rock formation, the drill bit simultaneously drills and creates the borehole. This allows the anchor bar to penetrate and self-drill into the ground, saving time and effort during installation. The self-drilling capability of these systems significantly increases their efficiency and makes them suitable for various ground conditions.
.jpg)
Versatility【Simultaneous Drilling, Grouting, and Anchoring】
Another notable feature of the self-drilling anchor system is its versatility. These systems are designed to be adaptable to a wide range of ground conditions, making them suitable for diverse applications. Whether it's securing slopes, stabilizing excavations, or reinforcing foundations, self-drilling anchor bolts can be customized to meet specific project requirements. The versatility of these systems stems from their ability to combine drilling, grouting and anchoring into a single process.
Traditional methods often require separate operations for drilling the borehole, injecting grout, and installing the anchor bars. This sequential approach can be time-consuming and may compromise the overall strength and integrity of the anchoring system. Self-drilling anchor systems streamline the process by connecting a hollow bar design with a self-drilling anchor bit. This simultaneous drilling, grouting, and anchoring not only saves time but also enhances the load-bearing capacity of the system. The injected grout ensures a tight bond between the anchor and the rock formation, significantly increasing the overall stability and durability of the structure.
Corrosion Resistance
Corrosion is one of the primary concerns when it comes to ground anchoring systems, especially in environments with high moisture or chemical exposure. Traditional anchoring systems, particularly those made of steel, are prone to corrosion over time, compromising their structural integrity and necessitating costly maintenance and replacements. Self-drilling anchor systems address this issue by incorporating corrosion-resistant materials in their design.
Anti-corrosion self-drilling anchor systems consists of the following products: stainless steel self-drilling anchor bolts, hot-dip galvanized self-drilling anchor bolts, epoxy-coated drilling anchor bolts, and double corrosion protection self-drilling anchor bolts. All of these products offer excellent resistance to corrosion, especially stainless steel, which makes it highly suitable for demanding environments. The material's composition includes a minimum of 10.5% chromium, which forms a passive oxide layer on the surface, protecting it from corrosion. This oxide layer self-heals when damaged, further enhancing the system's durability.
The passive oxide layer formed on the surface of anti-corrosion self-drilling anchor systems acts as a protective barrier against corrosive elements. This layer prevents direct contact between the metal and the surrounding environment, reducing the risk of corrosion. Additionally, the self-healing property of stainless steel ensures continuous protection even if the oxide layer is damaged. By preventing corrosion-related deterioration, these systems offer long-term stability and reliability. This longevity translates into reduced maintenance and replacement costs, making them a cost-effective solution for construction projects.
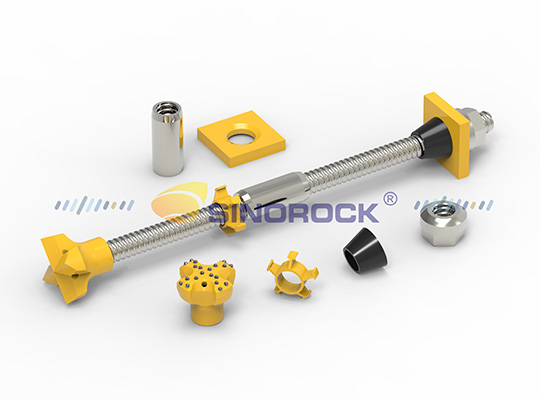
Conclusion
Self-drilling anchoring systems have become a preferred choice for rock anchoring applications due to their distinctive features. The ability to drill, grout, and anchor simultaneously, along with their self-drilling capability, revolutionizes the installation process, reducing time and costs. Furthermore, their corrosion resistance ensures long-term durability and reliability, making them an ideal choice for demanding environments. As the construction and mining industries continue to evolve, self-drilling anchoring systems will play a vital role in providing secure and efficient solutions for rock stabilization, further driving progress and innovation in these fields.
As a professional manufacturing self-drilling anchor bolts, Sinorock's team has many years of experience in providing complete geotechnical engineering services. If you have any needs or questions about anti-corrosion self-drilling anchor systems, please feel free to contact us at sinorock@sinorockco.com.
latest news
-
- 3 Crucial Factors That Impact the Quality of Self-Drilling Hollow Bolts
- Time:2025-01-26From:This Site
- As we all know, the quality of the self-drilling hollow bolts is vital to the whole project. It determines if the project is safe for the people in future use. Then, what will affect the quality of the self-drilling hollow bolts?
- View details
-
- Self-Drilling Anchor Bolt Construction in Complex Geological Slope
- Time:2025-01-24From:This Site
- During construction, Self-drilling hollow anchor bolt integrates drilling, grouting and anchoring functions, which significantly improves drilling efficiency. And under the action of pressure pump, the grouting in the rock strata and voids is full, which ensures the grouting thickness and anchoring effect.
- View details
-
- How Does Self-drilling Rock Bolt Drill in Quicksand Geological Condition?
- Time:2025-01-19From:This Site
- This in-depth guide explores how self-drilling rock bolts function in quicksand geological conditions, covering the challenges, construction methods, and best practices for ensuring effective anchorage in unstable, fluidic soil layers.
- View details
-
- Quality Control: the Vital Factor of A SDA Bolt Factory
- Time:2025-01-09From:This Site
- Sinorock’s comprehensive quality control system, from supplier management to outgoing inspections, ensuring the highest standards for self-drilling anchor bolts in construction.
- View details
-
- International Women's Day with Strawberry-picking
- Time:2024-03-09From:This Site
- Marked the annual observance of International Women's Day, and to commemorate this significant event, Sinorock organized a special strawberry-picking event exclusively for its female employees.
- View details
-
- Celebrate the 74th anniversary of the founding of the People's Republic of China
- Time:2023-10-01From:This Site
- On October 1st every year, we observe the annual National Day, commemorating the birth of our beloved motherland.
- View details
-
- SINOROCK to Attend EXPOMINA PERÚ 2024 in Lima, Peru
- Time:2024-08-10From:This Site
- Sinorock to Attend EXPOMINA PERÚ 2024 in Lima, Peru
- View details
-
- SINOROCK to Participate in MINING AND METALS CENTRAL ASIA 2024
- Time:2024-08-08From:This Site
- SINOROCK to Participate in MINING AND METALS CENTRAL ASIA 2024
- View details
-
- SINOROCK Gears Up for UGOL ROSSII & MINING 2024 with Custom Mining Solutions
- Time:2024-05-15From:This Site
- SINOROCK is thrilled to announce its participation in the highly anticipated 32nd International Trade Fair for Mining Technology, UGOL ROSSII & MINING 2024. The event will take place at the Exhibition complex "Kuzbass Fair" in Novokuznetsk, Kemerovo region - Kuzbass, Russia, from June 4th to 7th, 2024.
- View details