4 Methods of Tunnel Support: Ensuring Safety and Stability Underground
Time:2023-11-10From:sinorock View:
Tunnel construction has been a critical aspect of infrastructure development worldwide. From transportation tunnels to underground mines, the need for robust support methods is paramount. In this comprehensive article, we'll delve into four key methods of tunnel support: shotcrete support, rock bolts support, metal mesh support, and steel arch support. Our focus will be on the essential role of rock bolts in tunnel construction and their significance in ensuring the safety and stability of underground structures.The Importance of Tunnel Support
Before delving into the specific methods of tunnel support, it's essential to understand why tunnel support is critical. Tunnels are often built through challenging geological conditions, including rock masses and soil formations, which can be inherently unstable. In addition to this, the tunnels are exposed to a number of other external pressures such as water ingress and rockfalls. Without proper support, tunnels can collapse, leading to disastrous consequences. To meet these challenges and ensure the stability of the tunnel, engineers used a variety of support methods. These methods have evolved over the years to meet changing technical and construction needs.
1. Shotcrete Support
Shotcrete is a commonly used method for tunnel support. It mix cement, sand, stone, water and other materials needed in a certain proportion. After mixing evenly, spray them to the position where they need to be sprayed through the nozzle. The concrete is pneumatically projected at high velocity, adhering to the tunnel surface and forming a strong lining. Shotcrete support offers several advantages, including rapid application and flexibility in tunnel shapes. It is particularly effective in unstable geological conditions.
The construction of this method is simple. It is convenient and can quickly condense the sprayed place in a short time, effectively consolidating and waterproofing the tunnel.
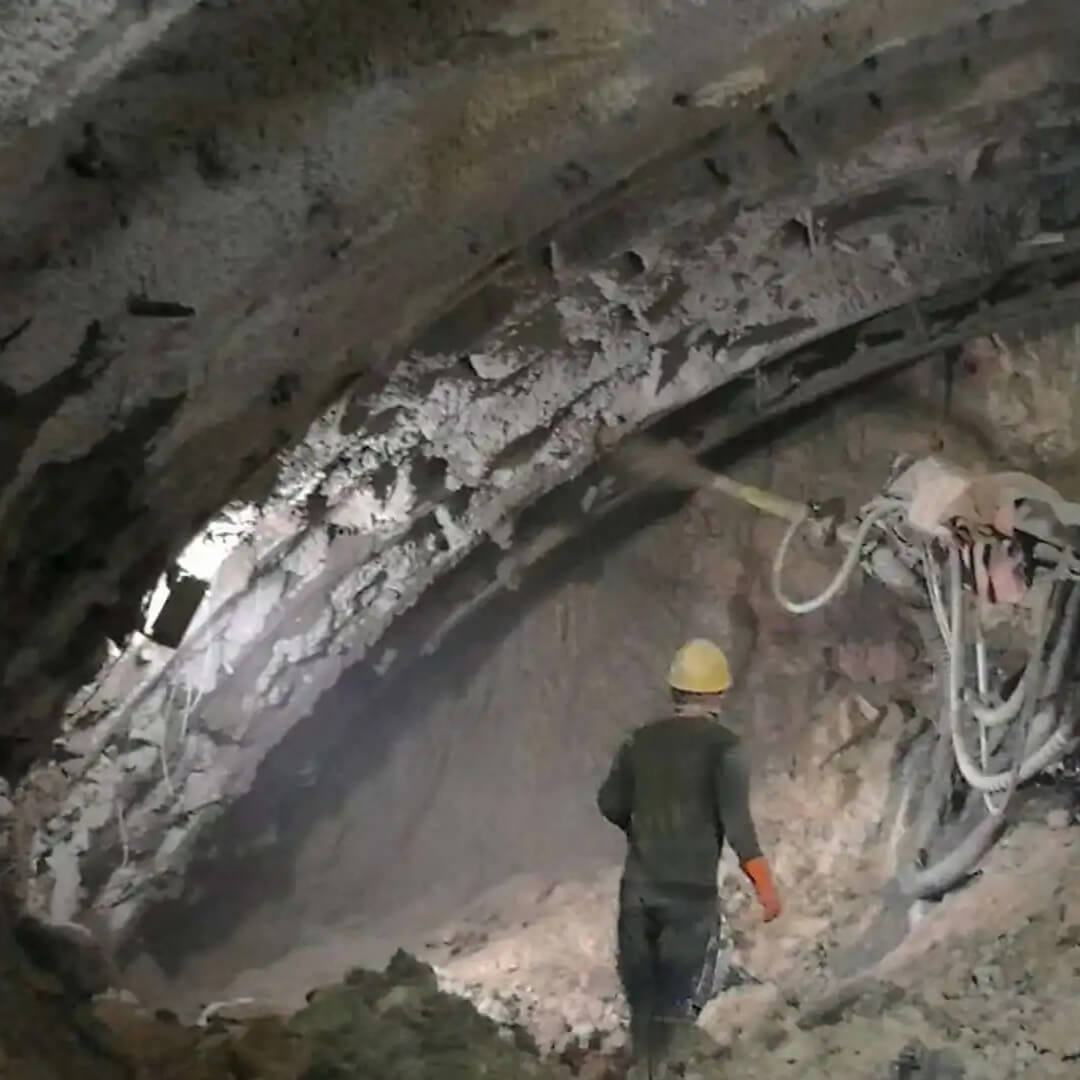
2. Metal Mesh Support
Metal mesh support is another method used to reinforce tunnel walls. Metal mesh, typically made of steel, is installed on the tunnel surface. This mesh provides additional support and helps prevent rockfalls and debris from entering the tunnel. Metal mesh support is often combined with other support methods for enhanced safety.
3. Steel Arch Support
Steel Arch supports are another essential method for tunnel reinforcement. These supports typically come in the form of steel ribs or arches that are installed within the tunnel. There are mainly steel types such as I-beam and grille arches. These arches distribute the load and provide stability to the tunnel structure. Steel arches are particularly useful in large-span tunnels and areas with challenging geological conditions. They offer a robust solution for maintaining tunnel integrity.
4. Rock Bolts Support
Now, let's dive deeper into rock bolts support, our primary focus in this article. Rock bolts are an integral part of tunnel support systems. They are long, threaded rods typically made of steel and are anchored into the surrounding rock to reinforce it. Rock bolts are essential in stabilizing rock masses and preventing collapses. Here's why they are crucial:
A. Ensuring Safety in Unstable Rock Conditions
In tunnels, especially in mining operations, unstable rock conditions are a constant concern. Rock bolts provide a means to anchor the rock in place, reducing the risk of rockfalls and collapses. The application of rock bolts creates a secure environment for tunnel workers and equipment.B. Support in Conjunction with Shotcrete
Rock bolts are often used in conjunction with shotcrete support. Shotcrete is applied to the tunnel walls, and rock bolts are installed to reinforce the shotcrete lining. This combination offers a high level of support and stability.
C. Types of Rock Bolts
There are various types of rock bolts available, each designed for specific conditions. These include self-drilling rock bolts, GFRP rock solid bolts, and forepiling pipe. The choice of rock bolt type depends on factors such as the rock's characteristics and the tunnel's design. In some complex and fractured terrain where it is difficult to make holes, we recommend the use of self-drilling hollow bar. This kind of hollow anchor bar adopts high-tensile alloy steel seamless steel pipe, the ultimate load and yield load can meet various complex geological conditions according to the design requirements. Moreover, the construction process of self-drilling rock bolt is relatively simple, and the rock bolt in the tunnel complete drilling, grouting and anchoring at one time, which simplifies the technological process and improves the construction efficiency.
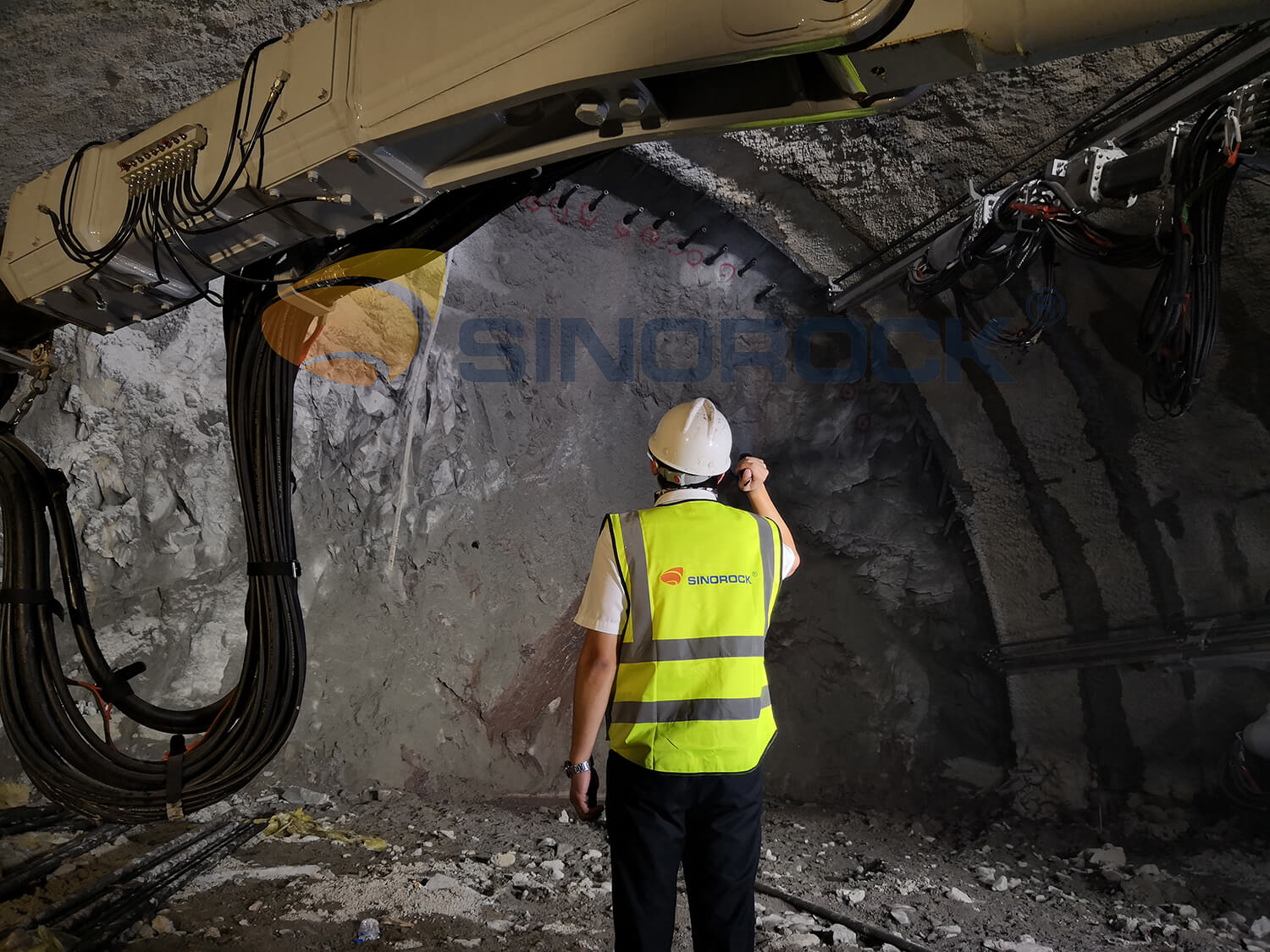
D. Improved Tunnel Durability
If the rock formation contains groundwater, the rock bolts in tunnel will be badly corroded by the environment so that the years of use will be reduced significantly. So most of the rock bolts used in tunnels are treated with corrosion protection, either hot-dip galvanized or coated with epoxy resin, or both. For example, Sinorock offers these duplex coating rock bolts. Rock bolts with anti-corrosion surface treatment can be used for permanent support in tunnels, which not only ensures safety, but also helps to improve the long-term durability of the tunnel.They help prevent deformation and cracking of the tunnel lining, extending the tunnel's lifespan.
Conclusion
In the world of tunnel construction, the choice of tunnel support method is crucial to ensure the safety and stability of these underground passageways. Understanding the importance of each of these methods and their applications is essential for engineers, contractors, and stakeholders involved in tunneling projects. As technology and research continue to advance, the industry can look forward to even more innovative solutions for tunnel support, ultimately making tunnels safer and more reliable for various applications.
Sinorock's dedication to excellence translates into safer, more efficient, and cost-effective construction processes. If you have any needs or questions about underground engineering, please feel free to contact us at sinorock@sinorockco.com.
latest news
-
- 3 Crucial Factors That Impact the Quality of Self-Drilling Hollow Bolts
- Time:2025-01-26From:This Site
- As we all know, the quality of the self-drilling hollow bolts is vital to the whole project. It determines if the project is safe for the people in future use. Then, what will affect the quality of the self-drilling hollow bolts?
- View details
-
- Self-Drilling Anchor Bolt Construction in Complex Geological Slope
- Time:2025-01-24From:This Site
- During construction, Self-drilling hollow anchor bolt integrates drilling, grouting and anchoring functions, which significantly improves drilling efficiency. And under the action of pressure pump, the grouting in the rock strata and voids is full, which ensures the grouting thickness and anchoring effect.
- View details
-
- How Does Self-drilling Rock Bolt Drill in Quicksand Geological Condition?
- Time:2025-01-19From:This Site
- This in-depth guide explores how self-drilling rock bolts function in quicksand geological conditions, covering the challenges, construction methods, and best practices for ensuring effective anchorage in unstable, fluidic soil layers.
- View details
-
- Quality Control: the Vital Factor of A SDA Bolt Factory
- Time:2025-01-09From:This Site
- Sinorock’s comprehensive quality control system, from supplier management to outgoing inspections, ensuring the highest standards for self-drilling anchor bolts in construction.
- View details
-
- International Women's Day with Strawberry-picking
- Time:2024-03-09From:This Site
- Marked the annual observance of International Women's Day, and to commemorate this significant event, Sinorock organized a special strawberry-picking event exclusively for its female employees.
- View details
-
- Celebrate the 74th anniversary of the founding of the People's Republic of China
- Time:2023-10-01From:This Site
- On October 1st every year, we observe the annual National Day, commemorating the birth of our beloved motherland.
- View details
-
- SINOROCK to Attend EXPOMINA PERÚ 2024 in Lima, Peru
- Time:2024-08-10From:This Site
- Sinorock to Attend EXPOMINA PERÚ 2024 in Lima, Peru
- View details
-
- SINOROCK to Participate in MINING AND METALS CENTRAL ASIA 2024
- Time:2024-08-08From:This Site
- SINOROCK to Participate in MINING AND METALS CENTRAL ASIA 2024
- View details
-
- SINOROCK Gears Up for UGOL ROSSII & MINING 2024 with Custom Mining Solutions
- Time:2024-05-15From:This Site
- SINOROCK is thrilled to announce its participation in the highly anticipated 32nd International Trade Fair for Mining Technology, UGOL ROSSII & MINING 2024. The event will take place at the Exhibition complex "Kuzbass Fair" in Novokuznetsk, Kemerovo region - Kuzbass, Russia, from June 4th to 7th, 2024.
- View details