Rock Bolt Corrosion Protection in Geotechnical Anchoring
Time:2023-09-22From:sinorock View:
Geotechnical anchoring is a widely used technology that has become one of the effective methods to improve geotechnical stability by utilizing the high tensile strength of steel to stabilize rock or soil layers. However, the durability of rock bolts is crucial in practical applications. The factors affecting the durability of rock anchor bars are material, construction process and environmental corrosion, among which the most influential is the corrosion of rock anchor bars caused by oxygen and water in the environment, which will have a serious impact on the service life of rock anchor bars and project cost. Therefore, effective protection of the anchor is an important part of ensuring the safety of the project.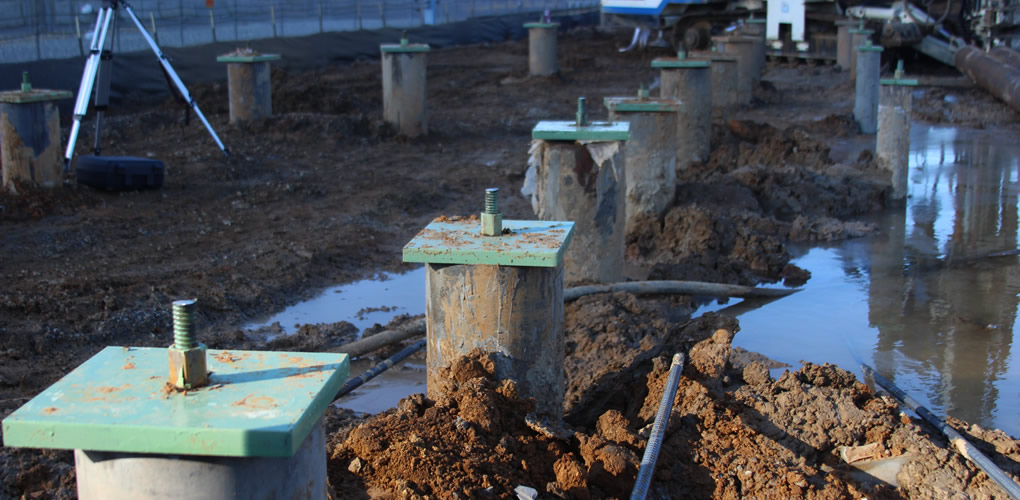
Causes of Rock Bolt Corrosion
There are three main reasons for the corrosion of rock bolts in geotechnical anchoring:
1. Changes in the composition of the local area of the metal surface, resulting in different potential differences, leading to corrosion.
2. The rupture of the oxide film on the metal surface is caused by inhomogeneity within the metal or loading of the metal, and corrosion occurs at the rupture. The different oxygen concentration in the soil layer makes different parts form different polarity, resulting in corrosion.
3. Changes in ionic concentration in the geological environment can also cause the rock anchor bar to generate batteries, leading to corrosion.
Anti-corrosion Method of Common Rock Bolt
The anti-corrosion method of common rock anchor bars can be divided into anchoring section anti-corrosion, free section anti-corrosion and exposed part anti-corrosion.
For the anchoring section, the general corrosive environment of the permanent rock bolt, the anchoring section of the rod body can be used in cement paste or mortar closed anti-corrosion, but the rod body must be surrounded by a 20mm thick protective layer. In severe corrosive environments permanent rock bolt, and its anchoring section within the rod body is appropriate to use corrugated pipe for external protection, pipe pores filled with epoxy resin or cement paste, casing around the thickness of the protective layer shall not be less than 10mm. The rod body of the anchored section of the temporary rock bolt should be closed with cement paste to prevent corrosion, and the thickness of the protective layer around the rod body shall not be less than 10mm.
For the free section, the rod body in the free section of the permanent rock bolt should be coated with lubricating oil or anticorrosion paint, then wrapped with a layer of plastic sheeting, and then coated with lubricating oil on the surface of the plastic sheeting, and then finally put into the plastic casing to form a double layer of anti-corrosion. The free section of the temporary anchor rod body can be coated with lubricant or anticorrosion paint, and then wrapped in plastic sheeting, etc., for simple anticorrosion measures.
For the exposed part, when the permanent rock bolt adopts an exposed head, it must be coated with anti-corrosion materials such as asphalt and then sealed with concrete, and the thickness of the protective layer of the exposed steel plate and anchorage shall not be less than 25mm; when sealing with cassette, it must be filled with lubricating oil to fill up the gap of the cassette. The anchor head of the temporary rock bolt is suitable to be anti-corrosion by bitumen.
Anti-corrosion Process and Advantages of Self-drilling Rock Bolts
Due to the increasing number of underwater tunnels across rivers and seas and mountain tunnels in corrosive underground environments, it has been difficult for ordinary mortar anchors to meet the corrosion resistance requirements of the supporting structures. Engineering practice shows that the corrosion of geotechnical anchors comes from air and groundwater, and the latter has a more obvious corrosive effect on rock bolts. Anchor corrosion in the stratum is dominated by chemical corrosion and scattered current corrosion, and the corrosive medium in the low layer acts on the outer surface of the anchor through the groundwater and air together, causing corrosion of the mortar and the rock bolts, which leads to anchorage failure.
As for the self-drilling rock bolt, is a hollow anchor bar that is itself both a drilling rod and an anchor rod, and can also be grouted through the hollow rod. The slurry is injected from the slurry hole of the drill bit, filling the cracks and holes of the stratum around the anchor rod from the inside out, making the anchor rod and the surrounding soil solidify as one, and playing a reinforcing role, which new type of support technology that combines the three major functions of drilling, grouting, and anchoring in one. Self-drilling hollow anchor bar does not need casing wall protection in construction, therefore, it is very suitable for the treatment of geological diseases such as loose and broken substrate prone to collapse holes, reinforcement of existing structures, grouting to fill cracks, and so on.
After the construction of a self-drilling hollow anchor bar, the slurry will be wrapped around the rod body, which can isolate the external environment to a certain extent, and play a certain anti-corrosion effect. However, this anti-corrosion effect depends on the fullness of the slurry, with uncertainty. Therefore, in the process of self-drilling hollow anchor bar production and processing, with professional anti-corrosion technology.
1. Epoxy Coating
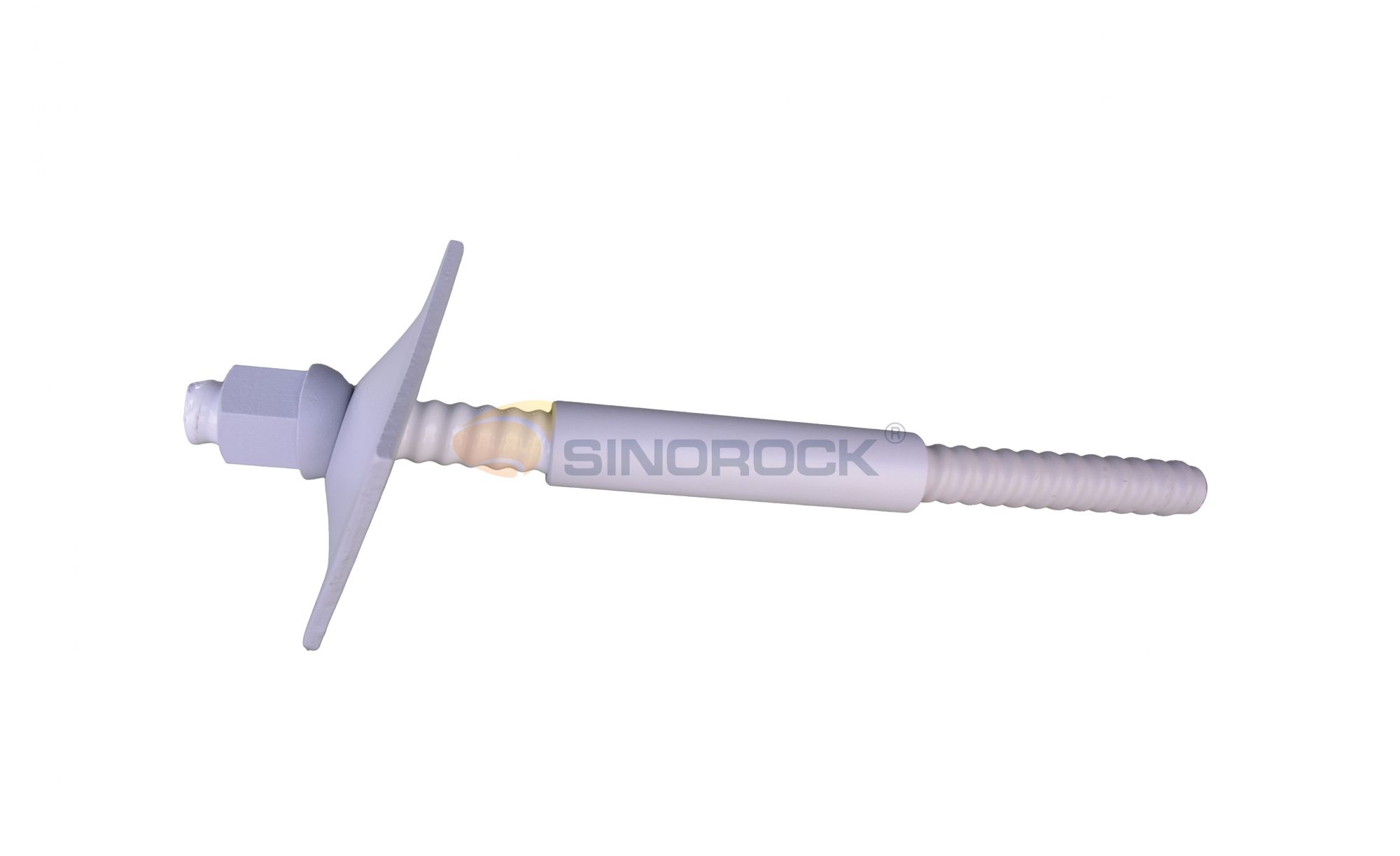
Epoxy coating is sprayed on the surface of the rod body, drill bit and other parts to isolate the parts from the outside world through the package of epoxy coating, so as to achieve the effect of anti-corrosion. This anti-corrosion process is mainly applicable to the ground and underground water containing sulfides and chlorides, seawater erosion occasions, as well as in the stray currents or aggressive media in the environment and so on.
2. Hot-dip Galvanizing Coating
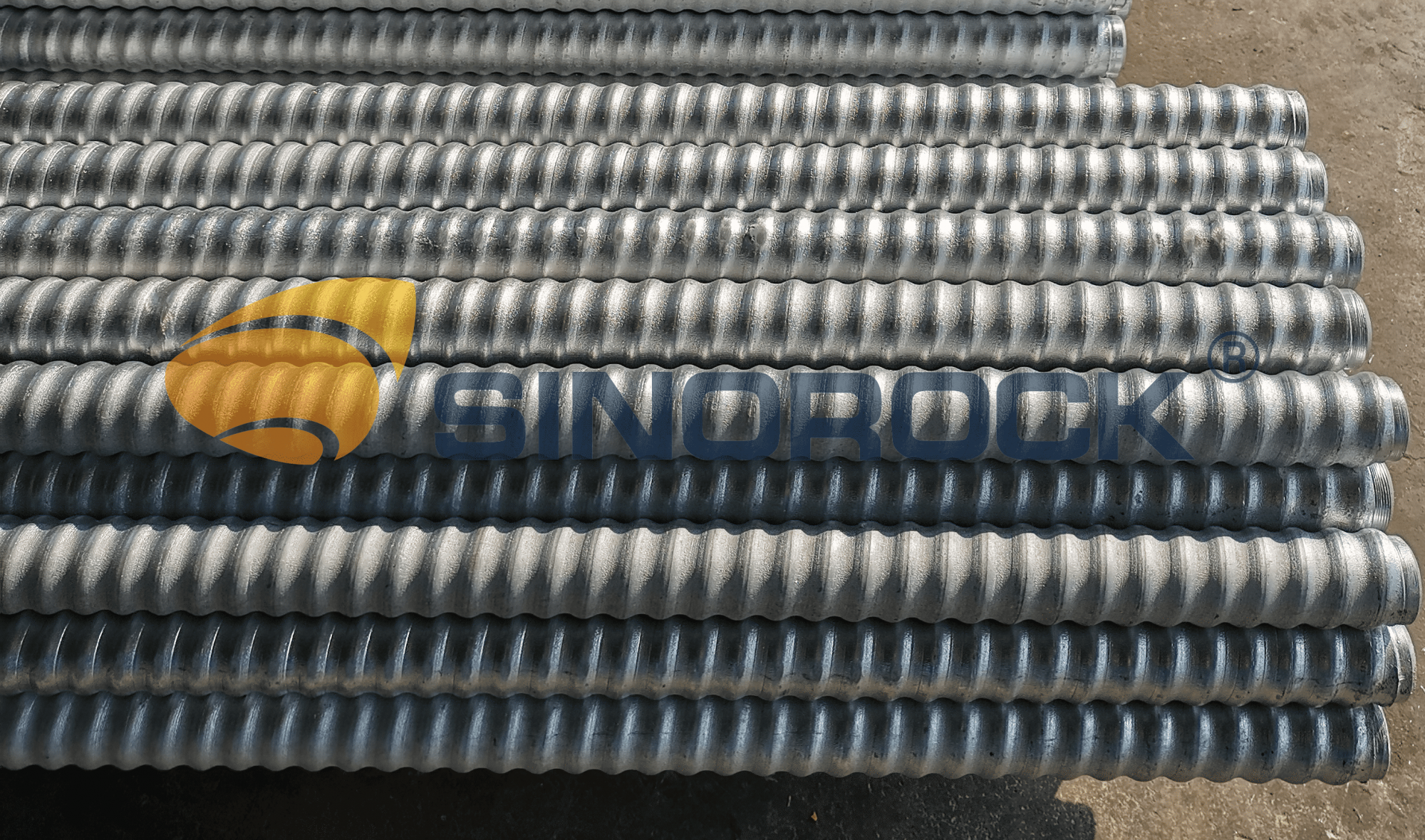
After the rod body, drill bit, coupler and other parts are processed and shaped, the surface is hot-dip galvanized by zinc plating process to prevent direct contact with the external environment on the parts, which can also prevent the parts from electrochemical corrosion. This anti-corrosion process is especially suitable for corrosive environments such as acid, alkali mist, and other corrosive environments, as well as geotechnical engineering fields with high requirements for service life and complex environments.
3. Double Corrosion Protection
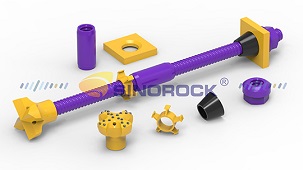
In the manufacture of the first steel parts for hot-dip galvanizing treatment, and then in its external surface and then spray epoxy coating. Comprehensive hot-dip galvanizing and epoxy coating are two anti-corrosion processes, forming a double layer of protection. This double corrosion protection self-drilling rock bolt has better anti-corrosion performance and longer service life, which can not only resist ordinary chemical corrosion, but also work under acidic environments and electrochemical corrosion of stray current.
Conclusion
Rock bolt corrosion prevention in geotechnical anchoring technology is crucial and affects the safety and durability of the project. Reasonable selection of materials, construction technology and professional anti-corrosion process is the key to ensuring the long-term reliability of anchor rods.
1. When choosing materials, prefer low carbon steel with reliable quality and good toughness as rock bolt material;
2. When installing anchor rods, try to avoid dry and wet alternating environments, and set up a drainage system to reduce the corrosion rate;
3. During construction, control the water-cement ratio or cement slurry concentration, and the cracks in the cement barrier should be less than 0.1mm, so as to improve the denseness and seepage resistance of the anchor solid. Special attention needs to be paid to the coupler of the rock bolt system where the grouting thickness may be affected.
4. If applied in the permanent construction environment, hot-dip galvanized or epoxy coating treatment can be adopted, and attention should be paid to the protection of coating during transportation or installation.
In actual application, suitable anti-corrosion measures need to be selected according to the specific construction environment and need to ensure the durability and service life of the rock bolt.
Sinorock's team has many years of experience in providing complete geotechnical engineering services. If you have any needs or questions about anti-corrosion self-drilling anchor systems, please feel free to contact us at sinorock@sinorockco.com.
latest news
-
- 3 Crucial Factors That Impact the Quality of Self-Drilling Hollow Bolts
- Time:2025-01-26From:This Site
- As we all know, the quality of the self-drilling hollow bolts is vital to the whole project. It determines if the project is safe for the people in future use. Then, what will affect the quality of the self-drilling hollow bolts?
- View details
-
- Self-Drilling Anchor Bolt Construction in Complex Geological Slope
- Time:2025-01-24From:This Site
- During construction, Self-drilling hollow anchor bolt integrates drilling, grouting and anchoring functions, which significantly improves drilling efficiency. And under the action of pressure pump, the grouting in the rock strata and voids is full, which ensures the grouting thickness and anchoring effect.
- View details
-
- How Does Self-drilling Rock Bolt Drill in Quicksand Geological Condition?
- Time:2025-01-19From:This Site
- This in-depth guide explores how self-drilling rock bolts function in quicksand geological conditions, covering the challenges, construction methods, and best practices for ensuring effective anchorage in unstable, fluidic soil layers.
- View details
-
- Quality Control: the Vital Factor of A SDA Bolt Factory
- Time:2025-01-09From:This Site
- Sinorock’s comprehensive quality control system, from supplier management to outgoing inspections, ensuring the highest standards for self-drilling anchor bolts in construction.
- View details
-
- International Women's Day with Strawberry-picking
- Time:2024-03-09From:This Site
- Marked the annual observance of International Women's Day, and to commemorate this significant event, Sinorock organized a special strawberry-picking event exclusively for its female employees.
- View details
-
- Celebrate the 74th anniversary of the founding of the People's Republic of China
- Time:2023-10-01From:This Site
- On October 1st every year, we observe the annual National Day, commemorating the birth of our beloved motherland.
- View details
-
- SINOROCK to Attend EXPOMINA PERÚ 2024 in Lima, Peru
- Time:2024-08-10From:This Site
- Sinorock to Attend EXPOMINA PERÚ 2024 in Lima, Peru
- View details
-
- SINOROCK to Participate in MINING AND METALS CENTRAL ASIA 2024
- Time:2024-08-08From:This Site
- SINOROCK to Participate in MINING AND METALS CENTRAL ASIA 2024
- View details
-
- SINOROCK Gears Up for UGOL ROSSII & MINING 2024 with Custom Mining Solutions
- Time:2024-05-15From:This Site
- SINOROCK is thrilled to announce its participation in the highly anticipated 32nd International Trade Fair for Mining Technology, UGOL ROSSII & MINING 2024. The event will take place at the Exhibition complex "Kuzbass Fair" in Novokuznetsk, Kemerovo region - Kuzbass, Russia, from June 4th to 7th, 2024.
- View details