How to Protect Self-Drilling Anchor Bars from Corrosion?
Time:2023-07-06From:sinorock View:
Self-drilling anchor bars are widely used in construction and civil engineering projects to provide stability and support to structures. Although anchor bars are buried in the soil, but also like any metallic element exposed to environmental conditions, are susceptible to corrosion.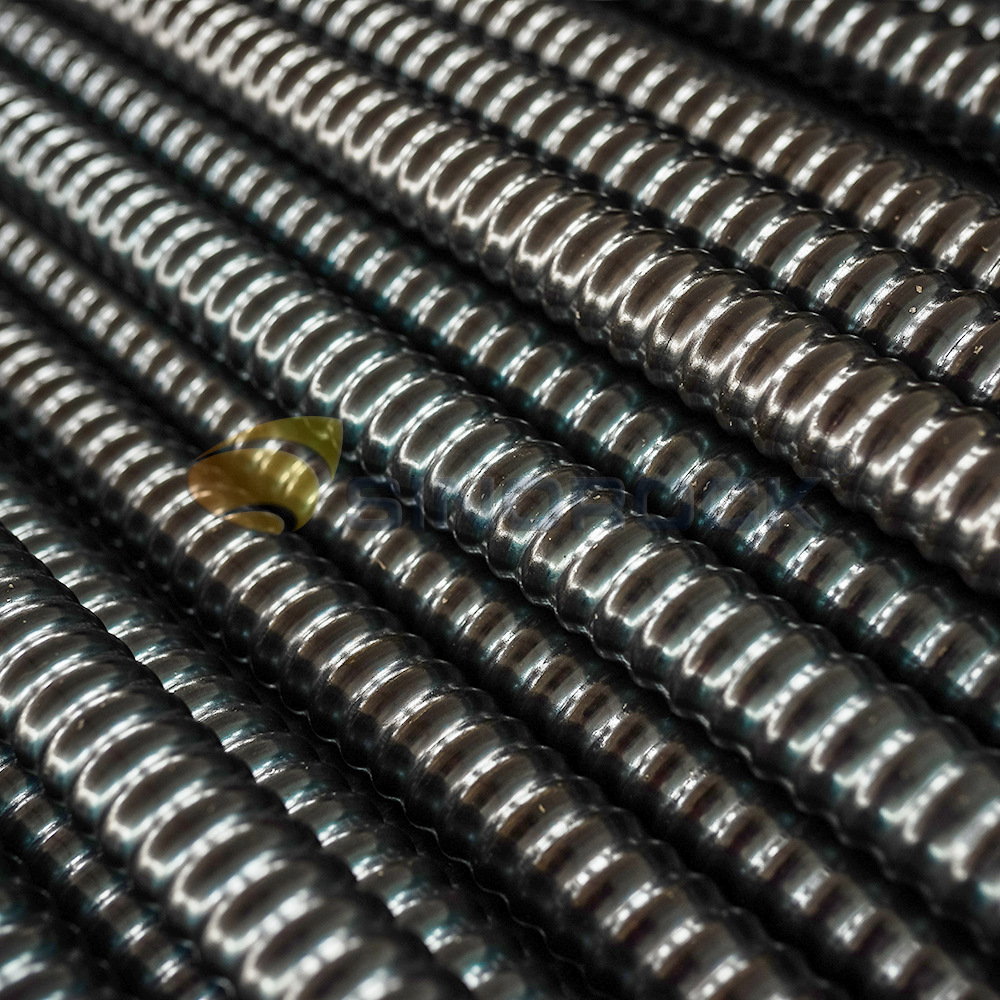
Conditions affecting the corrosion of self-drilling anchor bars
There are several conditions that can affect the corrosion of self-drilling anchor bars. For example, the factors of environmental conditions. The presence of moisture, humidity, and corrosive substances in the surrounding environment can accelerate the corrosion process. This is particularly true in coastal areas where saltwater or salt-laden air can cause corrosion. And human external factors. For example, physical damage to the protective coating or surface of the anchor bar can expose the underlying metal to corrosion. This can occur during installation, handling, or due to external factors such as impact or abrasion.
Corrosion not only weakens the structural integrity of anchor bars but also poses significant safety risks. Therefore, implementing effective measures to protect self-drilling anchor bars from corrosion is crucial.
Protect Self-Drilling Anchor Bars from Corrosion
1. Material Selection:
Choosing the right material for self-drilling anchor bars is the first line of defense against corrosion. Stainless steel, specifically austenitic stainless steel (e.g., AISI 304 and 316), is a popular choice due to its excellent corrosion resistance properties. Stainless steel anchor bars have a high chromium content, which forms a passive oxide layer that protects against corrosive elements.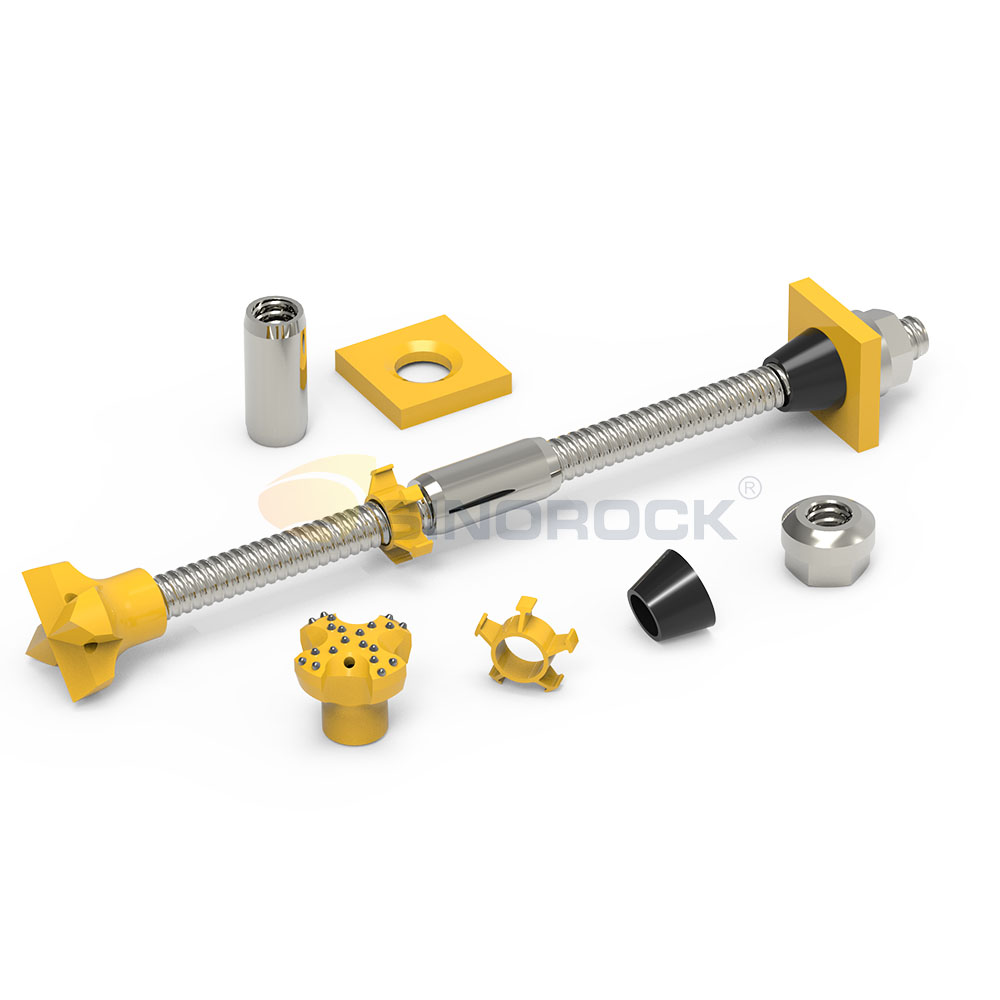
2. Coating and Surface Treatments:
Applying protective coatings or surface treatments is an effective way to enhance the corrosion resistance of self-drilling anchor bars. Epoxy coatings, polyurethane coatings, zinc coating, or other corrosion-resistant paints create a barrier between the metal surface and the corrosive environment. These coatings should be applied carefully, ensuring complete coverage of the anchor bars, including the threads, to prevent any vulnerable spots.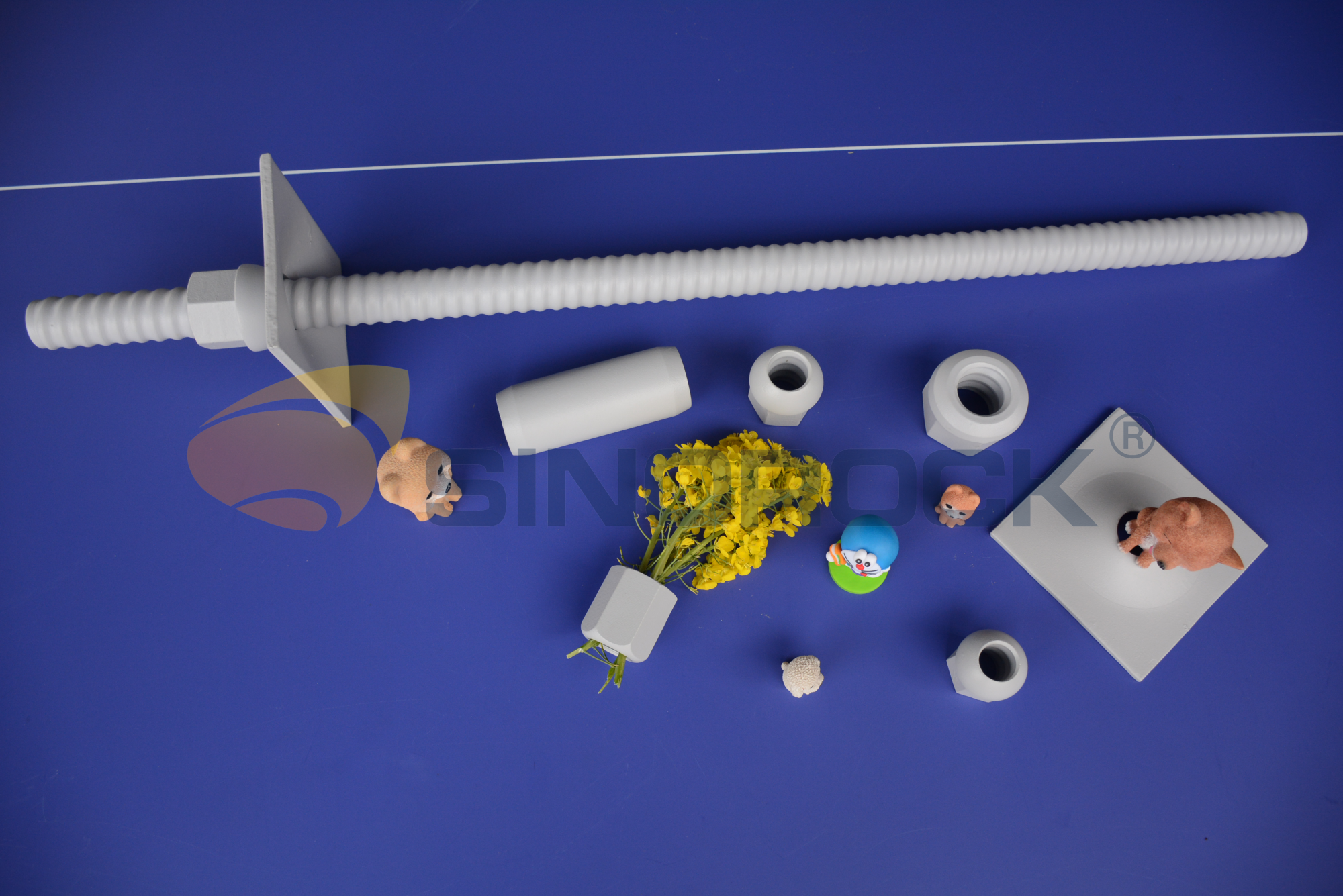
3. Cathodic Protection:
Cathodic protection is a widely used electrochemical technique to prevent corrosion in metallic structures. By creating an electric potential difference, cathodic protection diverts corrosion reactions from the anchor bars to a sacrificial anode or by applying an external electrical current. Sacrificial anodes, usually made of zinc or aluminum, are connected to the anchor bars, attracting corrosive elements and corroding themselves instead. In impressed current cathodic protection, a direct electrical current is applied to the anchor bars, protecting them from corrosion. Hot-dip galvanizing rock bolts are a perfect application of this technology.4. Proper Installation and Design:
Proper installation and design play a crucial role in preventing corrosion in self-drilling anchor bars. Attention should be given to the installing environmental conditions of the anchorage system to minimize exposure to corrosive environments. It is essential to ensure complete grouting around the anchor bar to prevent water ingress, which can lead to corrosion. Additionally, careful consideration should be given to the installation process, ensuring that all procedures are followed correctly to avoid damaging the protective coatings or compromising the integrity of the anchor bars.5. Regular Inspection and Maintenance:
Regular inspection and maintenance are essential to identify early signs of corrosion and take preventive measures. Inspections should be conducted periodically to check for any signs of rust, coating damage, or other forms of deterioration. If corrosion is detected, immediate action should be taken, such as repairing damaged coatings, replacing corroded sections, or implementing cathodic protection if necessary. It is crucial to follow the manufacturer's guidelines and industry standards for inspection and maintenance to ensure the long-term integrity of the anchor bars.Conclusion:
Protecting self-drilling anchor bars from corrosion is vital to maintain their structural integrity and ensuring the safety of construction and civil engineering projects. By selecting appropriate materials, applying protective coatings, implementing cathodic protection, following proper installation practices, and conducting regular inspections and maintenance, the lifespan of anchor bars can be significantly extended. Investing in corrosion prevention measures not only saves time and resources but also enhances the overall reliability and performance of the structures they support.Sinorock’s team has many years of experience in providing complete geotechnical engineering services. If you have any needs or questions about anti-corrosion self-drilling anchor systems, please feel free to contact us at sinorock@sinorockco.com.
latest news
-
- 3 Crucial Factors That Impact the Quality of Self-Drilling Hollow Bolts
- Time:2025-01-26From:This Site
- As we all know, the quality of the self-drilling hollow bolts is vital to the whole project. It determines if the project is safe for the people in future use. Then, what will affect the quality of the self-drilling hollow bolts?
- View details
-
- Self-Drilling Anchor Bolt Construction in Complex Geological Slope
- Time:2025-01-24From:This Site
- During construction, Self-drilling hollow anchor bolt integrates drilling, grouting and anchoring functions, which significantly improves drilling efficiency. And under the action of pressure pump, the grouting in the rock strata and voids is full, which ensures the grouting thickness and anchoring effect.
- View details
-
- How Does Self-drilling Rock Bolt Drill in Quicksand Geological Condition?
- Time:2025-01-19From:This Site
- This in-depth guide explores how self-drilling rock bolts function in quicksand geological conditions, covering the challenges, construction methods, and best practices for ensuring effective anchorage in unstable, fluidic soil layers.
- View details
-
- Quality Control: the Vital Factor of A SDA Bolt Factory
- Time:2025-01-09From:This Site
- Sinorock’s comprehensive quality control system, from supplier management to outgoing inspections, ensuring the highest standards for self-drilling anchor bolts in construction.
- View details
-
- International Women's Day with Strawberry-picking
- Time:2024-03-09From:This Site
- Marked the annual observance of International Women's Day, and to commemorate this significant event, Sinorock organized a special strawberry-picking event exclusively for its female employees.
- View details
-
- Celebrate the 74th anniversary of the founding of the People's Republic of China
- Time:2023-10-01From:This Site
- On October 1st every year, we observe the annual National Day, commemorating the birth of our beloved motherland.
- View details
-
- SINOROCK to Attend EXPOMINA PERÚ 2024 in Lima, Peru
- Time:2024-08-10From:This Site
- Sinorock to Attend EXPOMINA PERÚ 2024 in Lima, Peru
- View details
-
- SINOROCK to Participate in MINING AND METALS CENTRAL ASIA 2024
- Time:2024-08-08From:This Site
- SINOROCK to Participate in MINING AND METALS CENTRAL ASIA 2024
- View details
-
- SINOROCK Gears Up for UGOL ROSSII & MINING 2024 with Custom Mining Solutions
- Time:2024-05-15From:This Site
- SINOROCK is thrilled to announce its participation in the highly anticipated 32nd International Trade Fair for Mining Technology, UGOL ROSSII & MINING 2024. The event will take place at the Exhibition complex "Kuzbass Fair" in Novokuznetsk, Kemerovo region - Kuzbass, Russia, from June 4th to 7th, 2024.
- View details