Corrosion Protection of Rock Anchor Bolts: Ensuring Longevity in Support Projects
Time:2024-09-24From:sinorock View:
Rock anchor bolts are critical components in various construction and geotechnical projects, providing stability and support in tunnels, retaining walls, dams, and other infrastructure subjected to earth pressures. These systems are especially vital in challenging geological conditions, where soil and rock quality may be poor. However, despite their strength, rock anchor bolts are susceptible to degradation over time due to exposure to corrosive elements such as moisture, oxygen, and chemicals present in the environment.Corrosion, the gradual breakdown of metal due to chemical reactions with environmental agents, can severely compromise the integrity and lifespan of rock anchor bolts. Without appropriate corrosion protection, the performance of these systems may diminish, leading to structural failures, safety risks, and increased maintenance costs. In response, modern engineering practices have placed a significant emphasis on developing robust corrosion protection strategies tailored to the specific demands of each project. This article delves into the importance of corrosion protection for rock anchor bolts and explores various protection methods to ensure the longevity of support systems in construction projects.
Importance of Corrosion Protection in Rock Anchor Bolts
Corrosion is a natural process that occurs when metal reacts with oxygen, moisture, or other corrosive agents in the environment, forming oxides that weaken the metal structure. For rock anchor bolts, corrosion can lead to the following risks:
1. Structural Integrity Loss: As corrosion progresses, the strength of the anchor bolt reduces, compromising the stability of the structure it supports. This can result in partial or complete structural failure, especially in high-stress environments.
2. Increased Maintenance Costs: Corroded rock anchor bolts require frequent inspection, maintenance, and replacement, leading to increased operational costs over the lifespan of the project.
3. Reduced Lifespan: Corrosion accelerates the wear and tear of anchor bolts, reducing their service life and necessitating earlier-than-expected replacement, which is costly and often difficult in large-scale projects.
4. Safety Hazards: In critical infrastructure, such as tunnels, bridges, and retaining walls, the failure of rock anchor bolts due to corrosion can pose significant safety risks to both construction workers and the general public.
To prevent these issues, corrosion protection must be integrated into the design, selection, and installation of rock anchor bolts, considering both the environmental conditions and the required service life of the project.
Corrosion Protection Requirements for Rock Anchor Bolts in Support Projects
Rock anchor bolts can be categorized based on the duration of the support they provide: temporary, semi-permanent, and permanent. Each type of project has different corrosion protection requirements, depending on the expected lifespan and environmental conditions.
1. Temporary Support Projects
Temporary support projects typically have a lifespan of less than two years. These structures are often used during excavation, repair works, or to temporarily stabilize weak structures. Temporary support, commonly referred to as "shoring," is essential in construction to prevent collapses during active work.
In non-corrosive environments, temporary rock anchor bolts may not require corrosion protection, given their short-term use. However, when these projects are carried out in corrosive geological environments—such as areas with high moisture content, salinity, or chemical exposure—corrosion protection becomes crucial. In such cases, Level II corrosion protection is recommended. This level provides a moderate degree of protection suitable for environments where corrosion risks are present but not extreme.
For example, temporary supports in excavation sites near coastal areas or industrial zones might face saltwater or chemical exposure, which accelerates corrosion. In these instances, even though the project is short-term, investing in corrosion-resistant materials or coatings can prevent premature failure, ensuring safety and structural stability.
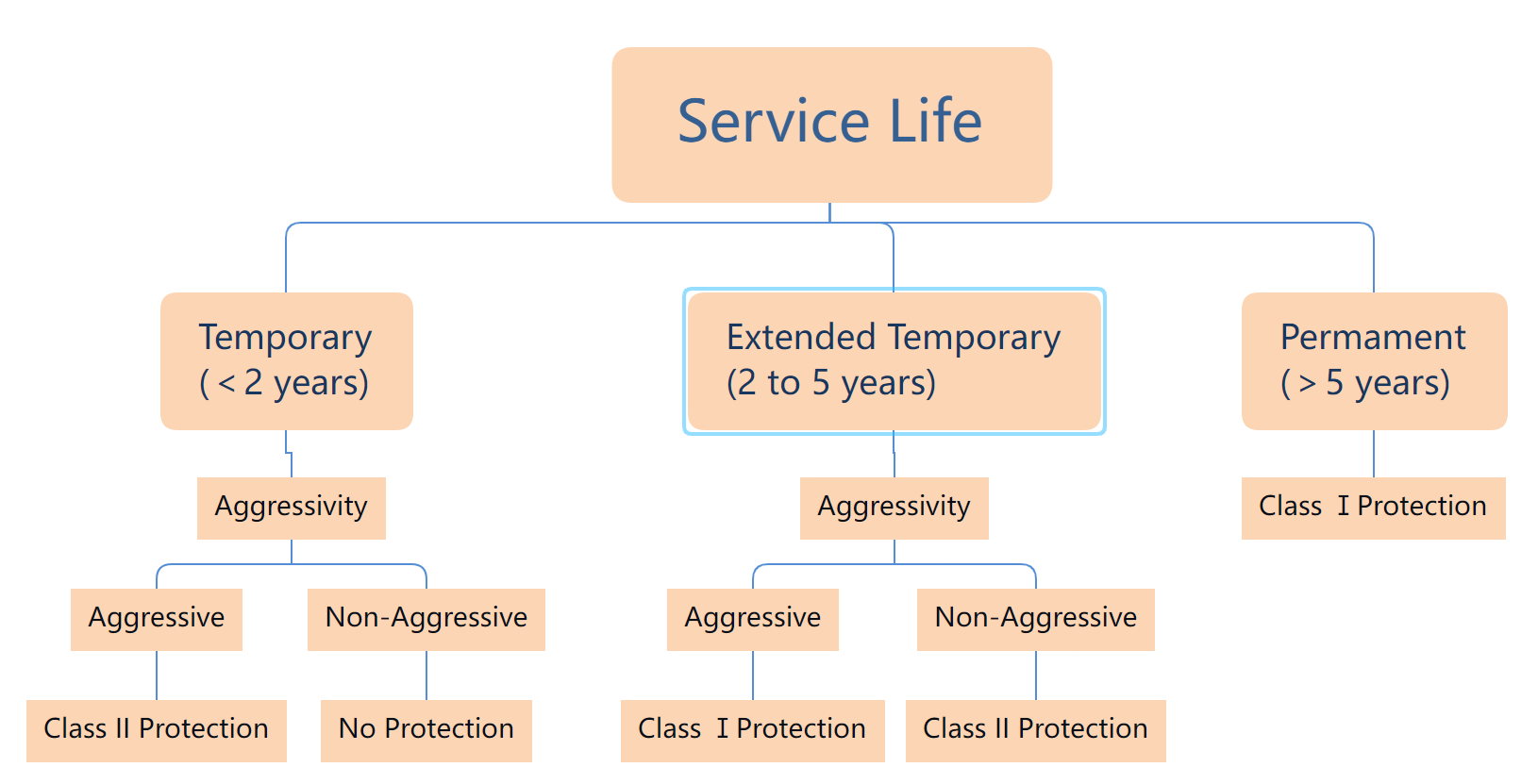
2. Semi-Permanent Support Projects
Semi-permanent support projects, with lifespans ranging between two and five years, require a more robust level of corrosion protection compared to temporary structures. These projects often occur in infrastructure development, where support is needed for a more extended period while permanent solutions are being constructed or during phased construction activities.In non-corrosive environments, Level II corrosion protection is often sufficient, as it provides an adequate barrier against environmental factors like oxygen and moisture. However, in corrosive environments, such as those with industrial pollutants, acidic soil, or stray electrical currents, Level I corrosion protection is necessary. This level ensures that the rock anchor bolts can withstand the harsh conditions without deteriorating.
Level I protection typically involves more comprehensive measures, such as the use of stainless steel or hot-dip galvanizing, which significantly extend the durability of the anchor bolts in challenging environments. These protection strategies are ideal for projects like tunnel excavation, where temporary supports may need to remain functional for several years before permanent structures are completed.
3. Permanent Support Projects
Permanent support projects are designed to last over five years, often extending to several decades. These projects require the highest level of corrosion protection due to the long-term nature of the support and the critical infrastructure involved. Examples include tunnels, dams, deep foundations, and retaining walls, where rock anchor bolts play a crucial role in ensuring stability and safety over the lifespan of the structure.
In such projects, Level I corrosion protection is mandatory, and it typically includes advanced methods like using stainless steel rock anchor bolts, hot-dip galvanizing, or double corrosion protection (DCP) techniques. These protection methods are chosen based on the specific environmental conditions and the required lifespan of the support system.
In highly corrosive environments, such as marine or industrial areas, where the structure is exposed to saltwater, chemicals, or other corrosive agents, using advanced materials like stainless steel or applying multiple layers of protection (e.g., galvanizing and epoxy coating) ensures that the anchor bolts can withstand both mechanical stress and environmental degradation over time.
Types of Corrosion Protection for Self-Drilling Anchor Bolts
Corrosion protection is a crucial consideration in the design and installation of self-drilling anchor bolts, particularly in harsh environments where exposure to corrosive agents is inevitable. The most common types of corrosion protection methods include stainless steel, hot-dip galvanizing, and double corrosion protection. These methods offer varying levels of protection, ensuring that anchor bolts can be adapted to the specific requirements of each support project.
1. Stainless Steel Self-Drilling Anchor Bolts
Stainless steel is known for its exceptional resistance to corrosion, making it a popular choice for permanent support projects. Stainless steel self-drilling anchor bolts are manufactured using high-grade alloys, such as 304 or 316 stainless steel, which possess inherent corrosion-resistant properties.
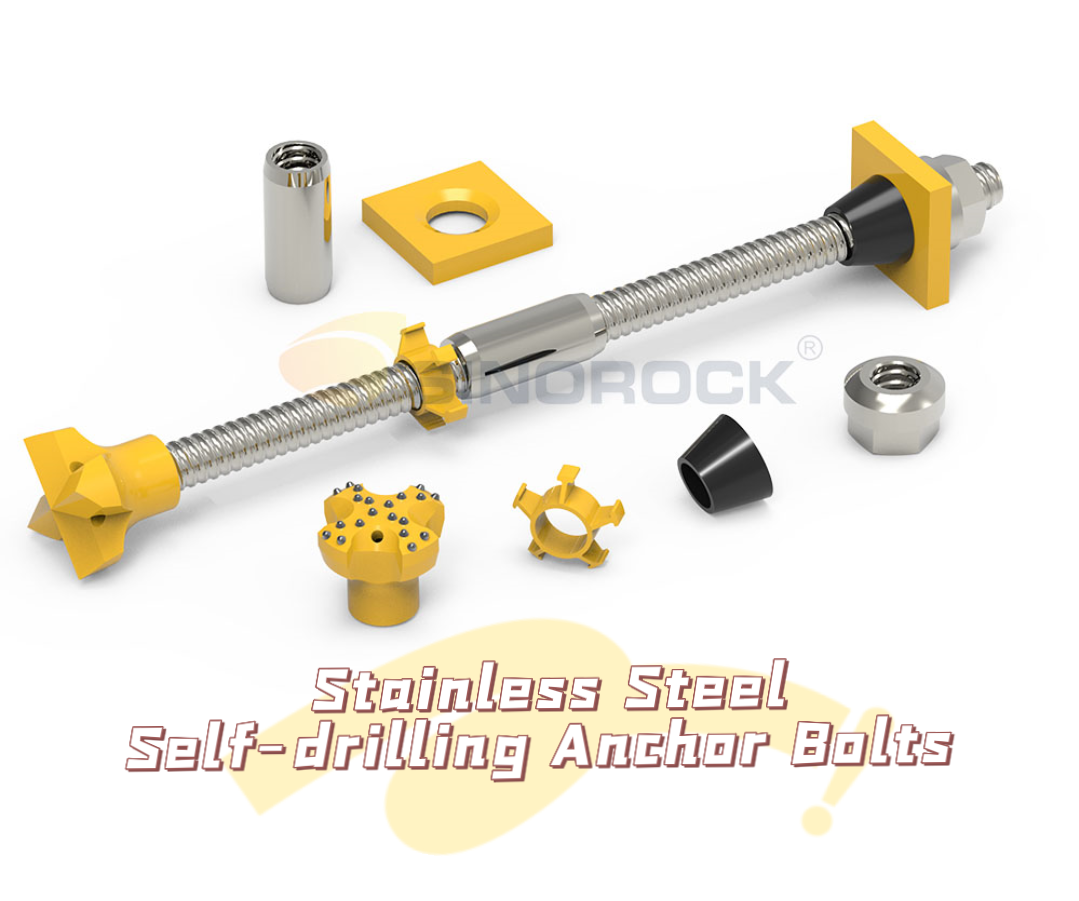
Advantages of Stainless Steel in Corrosion Protection
The primary advantage of stainless steel self-drilling anchor bolts lies in their ability to resist corrosion in a wide variety of environments. Stainless steel, especially grades such as 316, contains molybdenum, which enhances its resistance to pitting and crevice corrosion, especially in chloride-rich environments like marine settings. This makes stainless steel ideal for projects located near the coast or in areas where exposure to saltwater and moisture is a concern.
Another significant benefit is that stainless steel does not require additional coatings or treatments to maintain its corrosion resistance. Unlike other materials, which rely on external protective layers, stainless steel maintains its integrity even if scratched or damaged, making it highly reliable for long-term use in demanding conditions.
Applications of Stainless Steel Anchor Bolts
Due to their excellent corrosion resistance, stainless steel self-drilling anchor bolts are commonly used in permanent support projects where long-term durability is critical. These include tunnels, bridges, dams, and other infrastructure located in areas with aggressive environmental conditions. Additionally, stainless steel bolts are often specified for projects requiring the highest level of safety and reliability, such as nuclear power plants and other high-risk installations.
Limitations and Considerations
Despite its many advantages, stainless steel comes with a higher cost compared to other corrosion protection methods. The production of high-quality stainless steel is resource-intensive, which can make these bolts more expensive upfront. However, the long-term cost savings due to reduced maintenance and extended service life often outweigh the initial investment, especially for critical infrastructure projects.
2. Hot-Dip Galvanizing Self-Drilling Anchor Bolts
Hot-dip galvanizing is one of the most widely used corrosion protection methods for steel components, including self-drilling anchor bolts. This process involves immersing the steel bolts in molten zinc, which forms a protective coating that serves as a barrier against corrosive agents. The resulting zinc layer not only shields the steel from direct exposure to corrosive elements but also provides sacrificial protection, meaning that the zinc will corrode before the steel does.
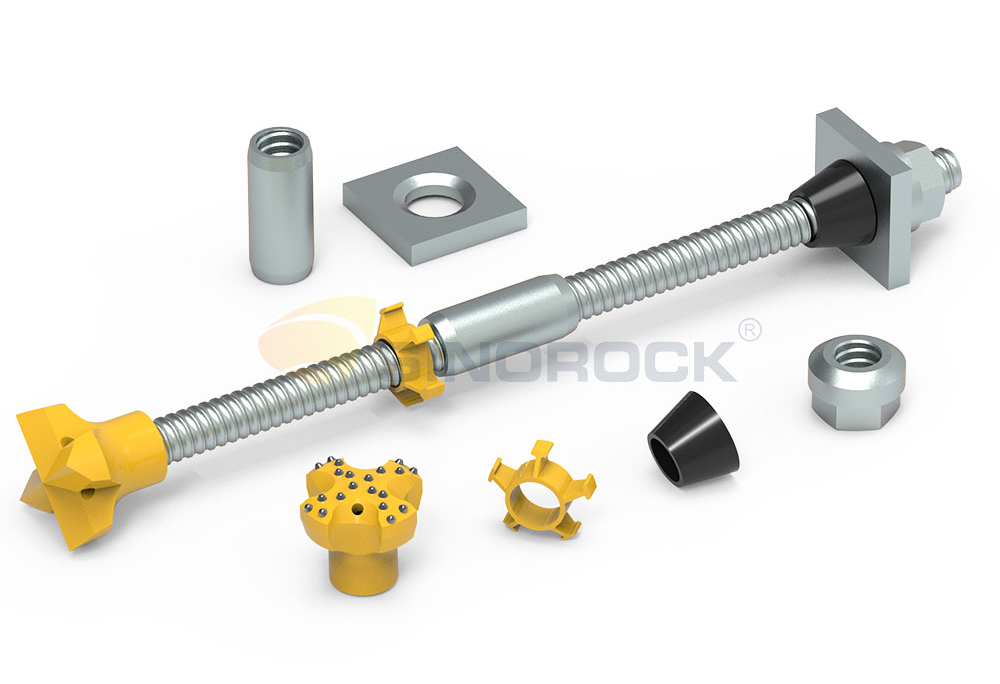
Advantages of Hot-Dip Galvanizing
The primary advantage of hot-dip galvanizing is its cost-effectiveness. It offers reliable corrosion protection at a fraction of the cost of stainless steel, making it an attractive option for projects with budget constraints. Additionally, hot-dip galvanizing creates a uniform and durable coating that adheres well to the steel surface, ensuring long-lasting protection.
Hot-dip galvanized self-drilling anchor bolts are particularly effective in environments with moderate exposure to corrosive agents, such as acid rain, saltwater spray, or industrial pollutants. They are commonly used in semi-permanent and permanent support projects where the environmental conditions are not as aggressive as those requiring stainless steel.
Applications of Hot-Dip Galvanized Anchor Bolts
Hot-dip galvanized self-drilling anchor bolts are frequently used in infrastructure projects such as roadways, railways, and building foundations. They are also popular in underground mining and tunneling, where the geological conditions may not warrant the use of more expensive stainless steel but still require a robust level of corrosion protection.
Limitations of Hot-Dip Galvanizing
One limitation of hot-dip galvanizing is that the zinc coating can wear down over time, especially in highly abrasive environments. Once the zinc layer is compromised, the underlying steel is vulnerable to corrosion. Therefore, this method is best suited for projects with moderate environmental exposure, or in combination with other protection methods like epoxy coatings for enhanced durability.
3. Double Corrosion Protection (DCP) Self-Drilling Anchor Bolts
Double corrosion protection (DCP) combines two protective layers—hot-dip galvanizing and an additional epoxy coating—to provide superior corrosion resistance. This dual-layer approach ensures that even in the most corrosive environments, the anchor bolts will maintain their structural integrity over time.
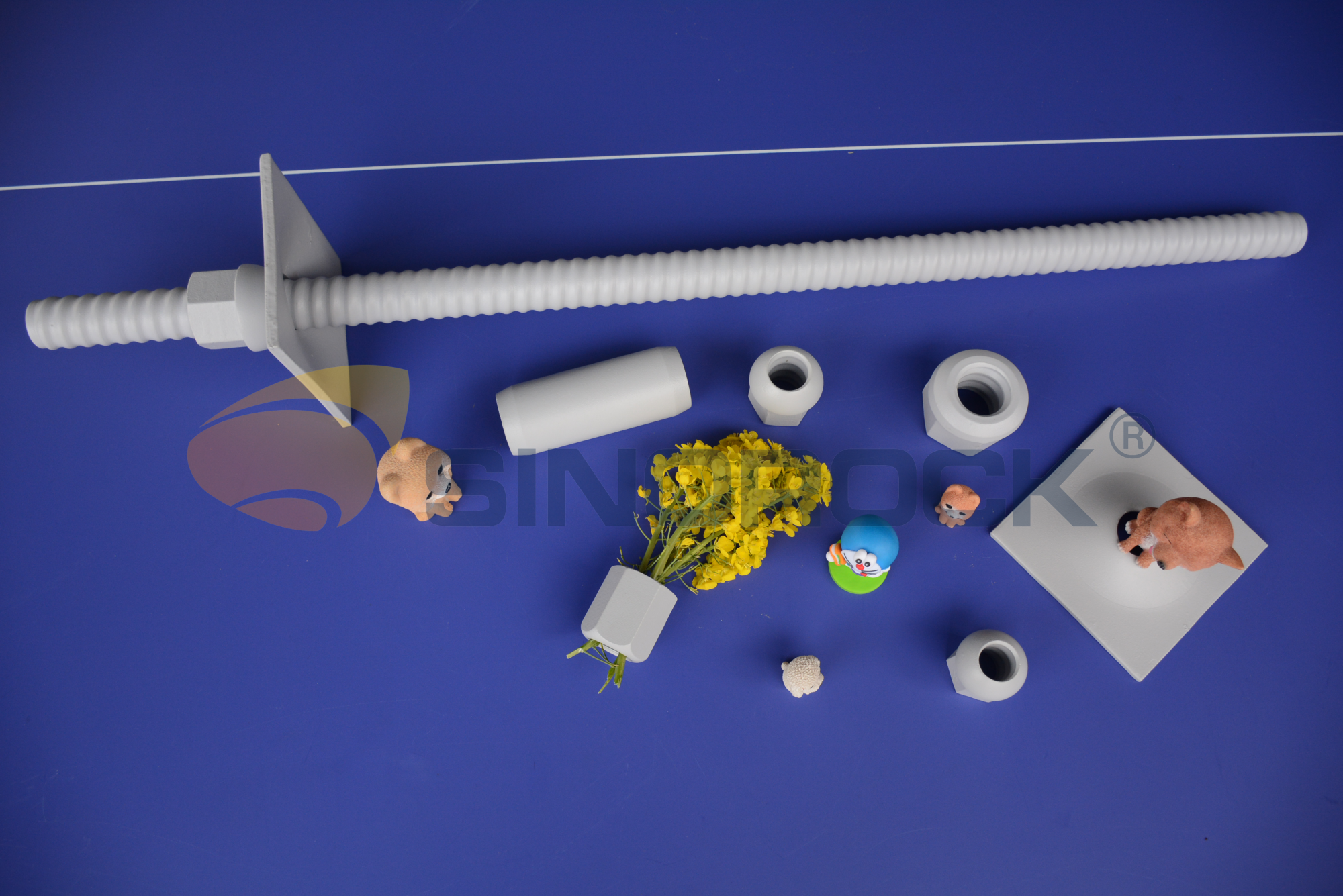
How Double Corrosion Protection Works
The first layer, hot-dip galvanizing, provides a base level of corrosion protection by coating the steel with a layer of zinc. This layer protects the steel from direct exposure to corrosive agents and offers sacrificial protection.
The second layer, an epoxy coating, is applied over the galvanized surface to provide an additional barrier. Epoxy coatings are highly resistant to a wide range of chemical agents, including acids, alkalis, and solvents, making them ideal for environments with aggressive chemical exposure. This double-layer system provides a belt-and-suspenders approach to corrosion protection, ensuring that even if one layer is compromised, the other remains intact.
Advantages of Double Corrosion Protection
Double corrosion protection offers the highest level of corrosion resistance, making it ideal for projects in extremely harsh environments, such as chemical plants, coastal areas, and areas with stray current corrosion. The combination of zinc and epoxy provides both sacrificial and barrier protection, ensuring the longevity of the anchor bolts even under the most challenging conditions.
Applications of DCP Anchor Bolts
Double corrosion protection self-drilling anchor bolts are used in high-risk environments where maximum durability and reliability are required. These bolts are commonly found in chemical processing plants, offshore oil rigs, and coastal infrastructure where exposure to corrosive agents is constant. They are also ideal for underground mining projects where the combination of water, salts, and chemicals can accelerate corrosion.
Considerations and Costs
While DCP anchor bolts offer unparalleled protection, they are also more expensive than single-layer protection methods. The additional manufacturing processes involved in applying both zinc and epoxy coatings contribute to the higher cost. However, for projects where failure due to corrosion is not an option, the additional cost is justified by the extended service life and reduced maintenance requirements of DCP anchor bolts.
Choosing the Right Corrosion Protection for Your Project
Selecting the appropriate corrosion protection for self-drilling anchor bolts depends on various factors, including the environmental conditions, the project’s lifespan, budget constraints, and the level of safety required. Careful consideration of these factors ensures optimal performance, durability, and cost-effectiveness. Here’s a guide to help in choosing the right corrosion protection method for your project:
1. Evaluate Environmental Conditions
The first step in selecting the right corrosion protection is to assess the environmental conditions in which the anchor bolts will be installed. Consider the following factors:
- Moisture Levels: Projects in wet or humid environments, such as tunnels, underground mines, and coastal areas, will benefit from stronger protection like stainless steel or double corrosion protection (DCP).
- Presence of Corrosive Agents: If the project is in an environment with high levels of chloride (marine environments), industrial pollutants, or chemicals, stainless steel or DCP will provide superior long-term resistance. For moderate exposure, hot-dip galvanizing may suffice.
- Temperature Fluctuations: Projects exposed to extreme temperature changes may experience material expansion and contraction, which can lead to micro-cracks in coatings. In such cases, using materials like stainless steel or DCP that can maintain integrity under stress is crucial.
2. Determine Project Lifespan and Durability Needs
- Permanent Support Structures: For projects that require permanent support, such as bridges, dams, or large tunnels, stainless steel or DCP self-drilling anchor bolts offer long-lasting protection and reduce the need for future maintenance. The initial investment is higher, but these materials ensure the structure's durability over decades.
- Semi-Permanent and Temporary Support: If the structure is intended to last only a few years, such as in temporary excavation support or short-term projects, hot-dip galvanized bolts may provide a sufficient balance between cost and protection.
3. Assess Budget and Cost Constraints
While corrosion protection is critical for safety and longevity, the project’s budget is often a limiting factor:
- Stainless Steel: This option is the most expensive due to the material cost and manufacturing process. However, it provides the best corrosion resistance for harsh environments and long-term projects, often justifying the higher upfront cost by reducing maintenance needs.
- Hot-Dip Galvanizing: A cost-effective alternative for projects in moderate environments, hot-dip galvanizing offers reliable protection at a lower cost than stainless steel, making it suitable for a wide range of applications where extreme conditions are not a concern.
- Double Corrosion Protection: While DCP offers the highest level of protection, the additional cost of applying both a zinc layer and epoxy coating can increase the overall project budget. DCP is ideal for projects where maximum protection is essential, such as in coastal or chemical environments, where failure due to corrosion is not acceptable.
4. Consider Maintenance and Long-Term Costs
The right corrosion protection should minimize the need for ongoing maintenance, which can significantly impact long-term project costs:
- Stainless Steel: Requires minimal maintenance due to its inherent corrosion resistance. Even if the surface becomes scratched, the material retains its protective properties, making it a good choice for reducing lifecycle costs.
- Hot-Dip Galvanizing: While more affordable, galvanized bolts may require regular inspections and potential recoating, especially in harsh environments. This maintenance cost should be factored into the overall budget.
- Double Corrosion Protection: Provides superior long-term protection, reducing the need for frequent maintenance, making it a cost-effective option for environments where regular repairs would be difficult or expensive.
5. Safety and Regulatory Considerations
Some projects, particularly in critical infrastructure like nuclear plants, bridges, or offshore platforms, may have strict safety regulations that dictate the use of specific corrosion protection methods. Stainless steel and DCP often meet the highest safety standards and are recommended for these types of applications. Compliance with international standards (such as ISO and ASTM) is often a requirement, ensuring the selected corrosion protection method is tested and reliable for the intended environment.
6. Work with Trusted Suppliers
Choosing high-quality materials from reputable suppliers is essential to ensuring that the corrosion protection methods perform as expected. Companies like Sinorock offer a wide range of self-drilling anchor bolts with various corrosion protection options, tailored to meet the unique needs of each project. Working with an experienced supplier ensures that you receive the best solution for your specific conditions, backed by industry expertise and reliable quality control.
Conclusion: Making the Right Decision
Choosing the right corrosion protection for your self-drilling anchor bolts is a decision that impacts the longevity, safety, and cost-efficiency of your project. By carefully assessing environmental factors, project lifespan, budget constraints, and maintenance requirements, you can select the optimal corrosion protection method that ensures the structural integrity of your project for years to come. Whether opting for stainless steel, hot-dip galvanizing, or double corrosion protection, working with trusted industry leaders like Sinorock guarantees access to the latest technology and materials, ensuring your project's success from start to finish.
latest news
-
- 3 Crucial Factors That Impact the Quality of Self-Drilling Hollow Bolts
- Time:2025-01-26From:This Site
- As we all know, the quality of the self-drilling hollow bolts is vital to the whole project. It determines if the project is safe for the people in future use. Then, what will affect the quality of the self-drilling hollow bolts?
- View details
-
- Self-Drilling Anchor Bolt Construction in Complex Geological Slope
- Time:2025-01-24From:This Site
- During construction, Self-drilling hollow anchor bolt integrates drilling, grouting and anchoring functions, which significantly improves drilling efficiency. And under the action of pressure pump, the grouting in the rock strata and voids is full, which ensures the grouting thickness and anchoring effect.
- View details
-
- How Does Self-drilling Rock Bolt Drill in Quicksand Geological Condition?
- Time:2025-01-19From:This Site
- This in-depth guide explores how self-drilling rock bolts function in quicksand geological conditions, covering the challenges, construction methods, and best practices for ensuring effective anchorage in unstable, fluidic soil layers.
- View details
-
- Quality Control: the Vital Factor of A SDA Bolt Factory
- Time:2025-01-09From:This Site
- Sinorock’s comprehensive quality control system, from supplier management to outgoing inspections, ensuring the highest standards for self-drilling anchor bolts in construction.
- View details
-
- International Women's Day with Strawberry-picking
- Time:2024-03-09From:This Site
- Marked the annual observance of International Women's Day, and to commemorate this significant event, Sinorock organized a special strawberry-picking event exclusively for its female employees.
- View details
-
- Celebrate the 74th anniversary of the founding of the People's Republic of China
- Time:2023-10-01From:This Site
- On October 1st every year, we observe the annual National Day, commemorating the birth of our beloved motherland.
- View details
-
- SINOROCK to Attend EXPOMINA PERÚ 2024 in Lima, Peru
- Time:2024-08-10From:This Site
- Sinorock to Attend EXPOMINA PERÚ 2024 in Lima, Peru
- View details
-
- SINOROCK to Participate in MINING AND METALS CENTRAL ASIA 2024
- Time:2024-08-08From:This Site
- SINOROCK to Participate in MINING AND METALS CENTRAL ASIA 2024
- View details
-
- SINOROCK Gears Up for UGOL ROSSII & MINING 2024 with Custom Mining Solutions
- Time:2024-05-15From:This Site
- SINOROCK is thrilled to announce its participation in the highly anticipated 32nd International Trade Fair for Mining Technology, UGOL ROSSII & MINING 2024. The event will take place at the Exhibition complex "Kuzbass Fair" in Novokuznetsk, Kemerovo region - Kuzbass, Russia, from June 4th to 7th, 2024.
- View details