Why is it important to choose a high quality nut for self-drilling anchor system?
Time:2023-05-31From:sinorock View:
The word "nut" is not unfamiliar to anyone. In our daily lives we see all kinds of nuts, such as hex nuts, hex flange nuts and cap nuts. A conventional nut is a component that is screwed together with a bolt or screw to provide a tightening effect. They are usually small, light and have metric threads. Unlike conventional nuts, this time we are talking about nuts used on self-drilling anchor systems.
Nuts used on anchor bolts are large and heavy compared to conventional nuts. It is a device with internal threads that transmits the anchoring force from the hollow anchor body to the plate and locks the plate in place, usually as the final step in the construction of a self-drilling anchor system.Why is it important to choose a good quality nut when using a self-drilling anchor system?
Nuts are used to lock the entire self-drilling anchor system to ensure that the entire system is fixed at the specified anchor point. Firstly, high quality nuts have better corrosion resistance and higher strength for long-term stable operation in harsh environments, whereas low quality nuts are prone to corrosion, cracking and other problems. Secondly, high quality nuts with standard values of the tensile strength of the corresponding anchor bars, which can withstand greater loads and provide stable mechanical properties, ensuring the stability and reliability of the anchor system as well as improving the durability of the anchor system; whereas a low quality nut destroys the balance of the mechanical properties of the entire anchor system and is prone to fatigue and fracture after prolonged use. Thirdly, high quality nuts have more precise design, high product accuracy, good quality and stronger fastening force, which can better ensure the solidity between the anchor bolt and the nut and avoid locking or loosening, thus ensuring the anchoring effect of the system. Therefore, when selecting a self-drilling anchor system, a nut of superior quality should be selected whenever possible.
Basic Knowledge of Nuts In SDA system
Definition of nuts in self-drilling anchor system
Installed at the end of the anchor bar, they prevent deformation of the rock by applying preload to transfer the anchoring force from the hollow anchor bar to the plate and compressing the plate to the rock face.
Features of nuts in self-drilling anchor system
One end is machined with a rounded surface, so that when there is a slight angle between the plate and the anchor bar, it can fit with the plate to ensure the transfer of force. If the angle is large, a domed nut or additional domed washer can be used.
Classification of nuts
By Name
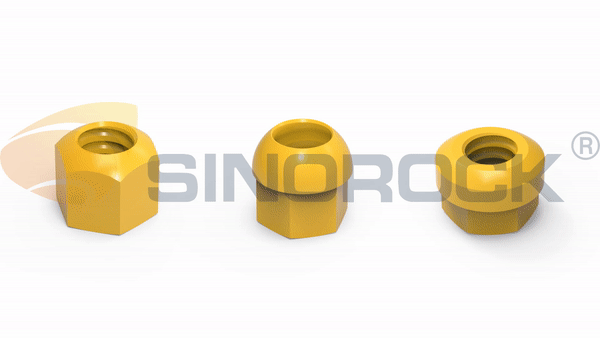
Item
Hex Nut
Domed Nut
Spherical Collar Nut
Usage
Mainly used in conjunction with flat plates for applications where the anchor is perpendicular to the support surface or at a small angle.
Mainly used in conjunction with the domed plates, when the anchor is at an angle to the support surface. In this case a larger bore plate is used, the domed nut/ spherical collar nut can form a line of contact with the bore of the plate. If hex nut are used, the contact will be incomplete and the nut may fall into the inner hole of the plate, affecting the support.
Applicable models
R25~R51、T30~T52、T76、T111
T-type except T76, T111
Item |
Hex Nut |
Domed Nut |
Spherical Collar Nut |
Usage |
Mainly used in conjunction with flat plates for applications where the anchor is perpendicular to the support surface or at a small angle. |
Mainly used in conjunction with the domed plates, when the anchor is at an angle to the support surface. In this case a larger bore plate is used, the domed nut/ spherical collar nut can form a line of contact with the bore of the plate. If hex nut are used, the contact will be incomplete and the nut may fall into the inner hole of the plate, affecting the support. |
|
Applicable models |
R25~R51、T30~T52、T76、T111 |
T-type except T76, T111 |
By Series
Series |
Coulomb X |
Coulomb S |
Coulomb E |
Coulomb C |
Materials |
316L/S460 and other special materials |
45#、QT500 |
Customized to customer requirements |
|
Rigidity |
/ |
Heat treatment |
No heat treatment |
|
Surface Treatment |
No surface treatment is required for 316L. S460:surface coating/galvanizing/double anti-corrosion coating |
Surface coating/galvanizing/double anti-corrosion coating |
Machining process of nuts
There are a number of different processes for nuts, including machining, forging and casting. Although each process has its own unique advantages and scope of application, most factories choose to use either 'forging' or 'casting'. So what is the difference between 'forging' and 'casting'?
Difference between Forging and Casting
Forging is the process of making a workpiece of a certain shape and size out of a metal material in a plastic state and changing its physical properties by means of hammering, etc.
Casting is a process in which metal is melted into a liquid and then poured into a mould, cooled and solidified, cleaned and then a casting of the required shape is obtained. Various types of objects with complex shapes can be made.
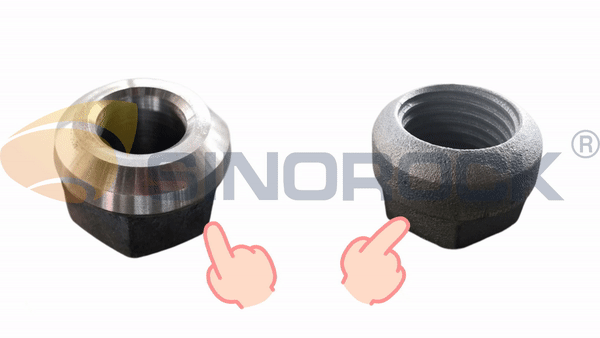
Comparison of the advantages and disadvantages of sand casting and forging processes
Processing Technic |
Advantages |
Limitations |
Sand casting |
1. Complex structural parts can be cast 2. Wide range of material sources and low cost |
1. Large number of work sequences and inconsistent quality 2. Defects (shrinkage, locking holes) tend to occur in castings |
Forging |
1. Refine grain size and improve strength 2. Reducing internal organizational weaknesses 3. Formation of a superficial layer of compact fibres to improve the toughness of the material |
1. High requirements for raw materials 2. No complex shapes can be processed |
Of course whether forging or casting is used, machining is required for subsequent processing and finishing to ensure the quality and accuracy of the nut.
Factors affecting the quality of the nut and the consequences caused
There are various factors that affect the quality of the nuts, mainly including materials, machining processes and design.
Faulty material
Resulting in a nut with reduced strength and performance not meeting design requirements
Unreasonable processing technology
Will cause the nut cracking, rolling fold, peeling and other problems make the nut performance is not up to standard, serious parts will cause scrap
Unreasonable process design
Resulting in the thread type, size and other non-standard requirements, will cause a bad spin; serious parts will be scrapped
What are the advantages of choosing the high quality nuts?
Excellent corrosion resistance
It is well known that the underground environment is very harsh and contains a variety of acids, alkalis and salts and other chemicals that tend to have a corrosive effect on anchor rods. High-quality nuts have a better corrosion resistance and can work steadily in harsh geographical conditions for a long time, avoiding damage or failure of the system.
Equal strength to the standard value of the corresponding anchor bar's tensile strength
The stability and reliability of the entire anchor system is ensured by the equal tensile strength of the nut and the anchor bar in the anchor system. High quality nuts and anchor bars can withstand greater loads and are less prone to fatigue and fracture after prolonged use, thus increasing the durability of the anchor system.
High precision and high tightening power
High-quality nuts are designed for precision, with high internal threads and machining accuracy. In use, the high quality nuts provide better tightening of the anchor bars and prevent loosening or locking, thus ensuring the stability and safety of the entire anchor system.
Low maintenance costs
Self-drilling anchor systems are often installed in difficult-to-reach underground locations. Therefore, if low quality nuts are used, it is likely that the nuts themselves will be damaged or fail, requiring more frequent maintenance and replacement, increasing maintenance costs and time. Choosing a high quality nut will significantly reduce later maintenance costs.
In conclusion, when using the self-drilling anchor system, good quality nuts should be selected wherever possible. This will ensure the stability and safety of the whole system, while reducing later-stage maintain expenses and providing better economic benefits and value for the owner. If you would like more information on this subject, please contact us. The most professional technical team at your disposal.
latest news
-
- 3 Crucial Factors That Impact the Quality of Self-Drilling Hollow Bolts
- Time:2025-01-26From:This Site
- As we all know, the quality of the self-drilling hollow bolts is vital to the whole project. It determines if the project is safe for the people in future use. Then, what will affect the quality of the self-drilling hollow bolts?
- View details
-
- Self-Drilling Anchor Bolt Construction in Complex Geological Slope
- Time:2025-01-24From:This Site
- During construction, Self-drilling hollow anchor bolt integrates drilling, grouting and anchoring functions, which significantly improves drilling efficiency. And under the action of pressure pump, the grouting in the rock strata and voids is full, which ensures the grouting thickness and anchoring effect.
- View details
-
- How Does Self-drilling Rock Bolt Drill in Quicksand Geological Condition?
- Time:2025-01-19From:This Site
- This in-depth guide explores how self-drilling rock bolts function in quicksand geological conditions, covering the challenges, construction methods, and best practices for ensuring effective anchorage in unstable, fluidic soil layers.
- View details
-
- Quality Control: the Vital Factor of A SDA Bolt Factory
- Time:2025-01-09From:This Site
- Sinorock’s comprehensive quality control system, from supplier management to outgoing inspections, ensuring the highest standards for self-drilling anchor bolts in construction.
- View details
-
- International Women's Day with Strawberry-picking
- Time:2024-03-09From:This Site
- Marked the annual observance of International Women's Day, and to commemorate this significant event, Sinorock organized a special strawberry-picking event exclusively for its female employees.
- View details
-
- Celebrate the 74th anniversary of the founding of the People's Republic of China
- Time:2023-10-01From:This Site
- On October 1st every year, we observe the annual National Day, commemorating the birth of our beloved motherland.
- View details
-
- SINOROCK to Attend EXPOMINA PERÚ 2024 in Lima, Peru
- Time:2024-08-10From:This Site
- Sinorock to Attend EXPOMINA PERÚ 2024 in Lima, Peru
- View details
-
- SINOROCK to Participate in MINING AND METALS CENTRAL ASIA 2024
- Time:2024-08-08From:This Site
- SINOROCK to Participate in MINING AND METALS CENTRAL ASIA 2024
- View details
-
- SINOROCK Gears Up for UGOL ROSSII & MINING 2024 with Custom Mining Solutions
- Time:2024-05-15From:This Site
- SINOROCK is thrilled to announce its participation in the highly anticipated 32nd International Trade Fair for Mining Technology, UGOL ROSSII & MINING 2024. The event will take place at the Exhibition complex "Kuzbass Fair" in Novokuznetsk, Kemerovo region - Kuzbass, Russia, from June 4th to 7th, 2024.
- View details