Anchor Bolts: 5 Essential Methods to Prevent Corrosion
Time:2024-01-10From:sinorock View:
I. Introduction
In the field of construction and civil engineering, geotechnical anchoring technology plays a pivotal role in ensuring the stability and safety of structures. Anchor bolts, made of steel, serve as the backbone of this technology by securing structures to rock or soil. The durability of anchor bolts becomes a critical factor in determining the long-term integrity of construction projects. Environmental corrosion, a significant challenge to durability, can potentially jeopardize the safety of structures and escalate construction costs.
II. Do anchor bolts rust?
A. Explanation of anchor bolt composition
Anchor bolts, crucial components in geotechnical anchoring, are typically constructed from steel. While steel provides robust strength, it is inherently susceptible to rust and corrosion.
B. Explanation of corrosion and its causes
Corrosion, a natural process, involves the gradual deterioration of materials, particularly metals, due to chemical reactions with their environment. In the context of anchor bolts, corrosion is chiefly fueled by the interaction of metal surfaces with moisture, oxygen, and other corrosive substances present in the geological environment.
C. Factors influencing anchor bolt corrosion
Numerous factors influence the corrosion of anchor bolts, ranging from the geological conditions of the installation site to the specific composition of the surrounding environment. Among the factors that can undermine the durability of anchor bolts, environmental corrosion stands out as the most significant threat. Environmental corrosion, primarily caused by groundwater interaction with metal materials, can lead to various forms of corrosion, including general corrosion, localized corrosion, and stress-induced corrosion. The consequences of anchor bolt corrosion can extend to compromising the safety of structures and increasing overall construction costs. To counter this challenge, it is essential to implement effective corrosion prevention methods.
III. Common Methods Coating for Corrosion Resistance
A. Explanation of Different Coating Options for Anchor Bolts
Anchor bolts, being exposed to diverse environmental conditions, demand robust corrosion-resistant coatings to ensure their longevity and structural integrity. Several coating options are available, each with unique characteristics tailored to specific requirements.
1. Hot-Dip Galvanizing:
Hot-dip galvanizing involves immersing anchor bolts in a bath of molten zinc, forming a zinc-iron alloy coating on the surface. This coating acts as an initial defense against corrosion. The process offers excellent protection in various environments, making it a popular choice for anchor bolts.
2. Epoxy Coating:
Epoxy coating provides an additional barrier against corrosive agents. It is usually applied as a second layer and complements the protection offered by hot-dip galvanizing. Epoxy coatings are known for their chemical resistance and durability, making them effective in environments with high moisture or chemical exposure.
3. Organic Coatings:
Organic coatings, such as polyurethane or polyethylene, provide a protective layer against corrosion. These coatings are often applied through painting or spraying methods. While not as robust as galvanizing, organic coatings are suitable for less aggressive environments and offer aesthetic appeal.
B. Application Techniques for Optimal Protection
The effectiveness of corrosion-resistant coatings relies not only on the type of coating selected but also on the application techniques employed. Proper application ensures uniform coverage and adherence, maximizing the coating's protective capabilities.
1. Surface Preparation:
Before applying any coating, thorough surface preparation is crucial. Cleaning, degreasing, and removing any existing contaminants ensure proper adhesion of the coating to the anchor bolts.
2. Temperature and Humidity Considerations:
The application of coatings is sensitive to environmental conditions. Ideal temperatures and humidity levels must be maintained during the application process to prevent issues such as incomplete curing or poor adhesion.
3. Thickness Control:
Monitoring and controlling the thickness of the applied coating is essential. Coatings that are too thin may not provide adequate protection, while excessively thick coatings can lead to issues such as cracking or peeling.
4. Quality Assurance:
Implementing a comprehensive quality assurance process ensures that the coating meets specified standards. Regular inspections, adherence to industry guidelines, and quality control checks contribute to the overall effectiveness of the corrosion protection strategy.
In summary, choosing the best coating for anchor bolts involves a nuanced understanding of the specific project requirements and environmental conditions. Each coating option has its merits and limitations, and a tailored approach, combined with meticulous application techniques, is key to optimizing corrosion resistance and ensuring the long-term performance of anchor bolts.
IV. Five common methods of corrosion protection
A. Understand the Corrosive Nature of the Geological Environment
The first step in preventing anchor bolt corrosion is to thoroughly understand the geological environment in which the anchor bolts will be installed. Different geological conditions can expose anchor bolts to varying levels of corrosive agents, such as moisture and chemical compounds. Conducting a comprehensive geological assessment allows engineers and construction professionals to identify potential corrosion risks and implement appropriate preventive measures. By understanding the corrosive nature and degree of the geology, it becomes possible to select the most suitable anchor bolt materials and corrosion-resistant coatings.
B. Utilize Duplex Coating Anti-Corrosion in Aggressive Formations
In environments characterized by aggressive geological formations or high corrosion potential, duplex coating anti-corrosion is a highly effective method. This technique involves applying two layers of protective coatings to the anchor bolts. The first layer typically consists of hot-dip galvanizing, where the anchor bolts are immersed in a bath of molten zinc. This process creates a zinc-iron alloy coating on the surface of the anchor bolts, providing an initial level of protection against corrosion. The second layer involves the application of an epoxy coating, which adds an additional barrier against corrosive agents. The combined effect of these coatings significantly enhances the anchor bolts' resistance to corrosion. It is essential to ensure that the thickness of the cement slurry protective layer is not less than 20 mm in aggressive formations to provide adequate protection.
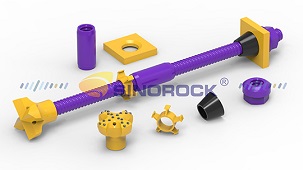
C. Prefer Pressure-dispersive Anchors
Pressure-dispersive anchors are an effective choice for mitigating the risk of corrosion in anchor bolts. These anchors are designed to distribute loads over a broader area, reducing localized stress concentrations that can lead to corrosion. By spreading the load more evenly, pressure-dispersive anchors help to minimize the risk of stress-induced corrosion, which is a common problem in anchor bolt systems. This method not only enhances the anchor bolts' structural integrity but also contributes to their long-term corrosion resistance.
D. Opt for Anchor Rods with Prestressed Ribs
To further improve corrosion resistance, consider using anchor rods with prestressed ribs made of steel wire and steel hinge wire. Prestressing the ribs can help distribute loads more evenly and reduce the risk of corrosion-induced stress cracking. It is crucial to ensure that the locking load on these anchor rods does not exceed 60% of the standard value of the tensile strength of the rib material. This precautionary measure helps maintain the structural integrity of the anchor rods while minimizing the risk of corrosion-related issues.
E. Properly Seal Gaps Between Hollow Bar Joints
In construction involving hollow bar anchor bolts, maintaining a tight seal between the joints of the hollow bar and the drill bit is essential for preventing corrosion. Any gaps or voids in these joints can provide pathways for moisture, oxygen, and corrosive substances to penetrate the anchor system. To prevent this, it is imperative to ensure that the gap between the joint of the hollow bar and the bit is properly refilled and sealed. Regular inspections and maintenance are essential to identify and address any gaps that may develop over time.
V. Conclusion
Corrosion prevention measures are crucial for ensuring the success of construction projects that rely on geotechnical anchoring applications. By understanding the geological environment, using duplex coating anti-corrosion, employing pressure dispersion anchors, opting for anchor rods with prestressed ribs, and maintaining proper sealing of hollow bar joints, construction professionals can significantly enhance the corrosion resistance of anchor bolts.
At Sinorock, we have dedicated our efforts to researching anti-corrosion methods for anchor bolts in order to meet the demands of our customers. Our double corrosion protection self-drilling anchor bolts effectively address the issue of groundwater and chemical medium corrosion in permanent support projects, such as hydropower stations and tunnels. Our products have been successfully exported to over 40 countries across continents6 continents and have been widely utilized in slope, foundation, and tunnel engineering. If you have any inquiries, please feel free to contact us at sinorock@sinorockco.com.
latest news
-
- 3 Crucial Factors That Impact the Quality of Self-Drilling Hollow Bolts
- Time:2025-01-26From:This Site
- As we all know, the quality of the self-drilling hollow bolts is vital to the whole project. It determines if the project is safe for the people in future use. Then, what will affect the quality of the self-drilling hollow bolts?
- View details
-
- Self-Drilling Anchor Bolt Construction in Complex Geological Slope
- Time:2025-01-24From:This Site
- During construction, Self-drilling hollow anchor bolt integrates drilling, grouting and anchoring functions, which significantly improves drilling efficiency. And under the action of pressure pump, the grouting in the rock strata and voids is full, which ensures the grouting thickness and anchoring effect.
- View details
-
- How Does Self-drilling Rock Bolt Drill in Quicksand Geological Condition?
- Time:2025-01-19From:This Site
- This in-depth guide explores how self-drilling rock bolts function in quicksand geological conditions, covering the challenges, construction methods, and best practices for ensuring effective anchorage in unstable, fluidic soil layers.
- View details
-
- Quality Control: the Vital Factor of A SDA Bolt Factory
- Time:2025-01-09From:This Site
- Sinorock’s comprehensive quality control system, from supplier management to outgoing inspections, ensuring the highest standards for self-drilling anchor bolts in construction.
- View details
-
- International Women's Day with Strawberry-picking
- Time:2024-03-09From:This Site
- Marked the annual observance of International Women's Day, and to commemorate this significant event, Sinorock organized a special strawberry-picking event exclusively for its female employees.
- View details
-
- Celebrate the 74th anniversary of the founding of the People's Republic of China
- Time:2023-10-01From:This Site
- On October 1st every year, we observe the annual National Day, commemorating the birth of our beloved motherland.
- View details
-
- SINOROCK to Attend EXPOMINA PERÚ 2024 in Lima, Peru
- Time:2024-08-10From:This Site
- Sinorock to Attend EXPOMINA PERÚ 2024 in Lima, Peru
- View details
-
- SINOROCK to Participate in MINING AND METALS CENTRAL ASIA 2024
- Time:2024-08-08From:This Site
- SINOROCK to Participate in MINING AND METALS CENTRAL ASIA 2024
- View details
-
- SINOROCK Gears Up for UGOL ROSSII & MINING 2024 with Custom Mining Solutions
- Time:2024-05-15From:This Site
- SINOROCK is thrilled to announce its participation in the highly anticipated 32nd International Trade Fair for Mining Technology, UGOL ROSSII & MINING 2024. The event will take place at the Exhibition complex "Kuzbass Fair" in Novokuznetsk, Kemerovo region - Kuzbass, Russia, from June 4th to 7th, 2024.
- View details