The Application of Self-Drilling Hollow Anchor Bar in IV-V Class Surrounding Rock Tunnel
Time:2024-06-26From:sinorock View:
Introduction
In modern tunnel construction, dealing with complex geological conditions is a significant challenge, particularly when working with surrounding rocks of IV-V class. These rocks are typically characterized by a loose, blocky structure, high water content, and instability, which pose substantial risks to the progress and quality of the project, and even to the safety of the construction workers. Efficient and reliable support methods are essential to address these issues. Traditional methods, such as mortar anchor bolts and ductule supports, often fall short due to difficulties in drilling, grouting, and ensuring the durability of the anchors. However, the introduction of self-drilling hollow anchor bars has revolutionized tunnel support systems, offering a more efficient, reliable, and safer solution. This article delves into the application of self-drilling hollow anchor bars in IV-V class surrounding rock tunnels, exploring their benefits, working principles, and real-world applications.
Challenges of IV-V Class Surrounding Rock Tunnels
Geological Characteristics
IV-V class surrounding rocks are typically found in areas with developed bedding joints and significant water inflow. These rocks are usually composed of loose, fragmented materials that are prone to collapse and deformation. The presence of water further exacerbates these issues by reducing the cohesion between rock particles and increasing the overall instability of the rock mass. These conditions present several challenges for tunnel construction, including:
- Loose Blocky Structure: The fragmented nature of the rocks makes them prone to displacement and collapse during excavation.
- Water Ingress: Significant water inflow can lead to further weakening of the rock mass, creating a mix of mud and loose debris that complicates construction efforts.
- Stability Issues: The combination of loose structure and water saturation results in poor stability, making it difficult to maintain the integrity of the tunnel during and after construction.
Traditional Support Methods and Their Limitations
Traditional support methods, such as the use of mortar anchor bolts and ductules, have several limitations when applied to IV-V class surrounding rocks:
- Drilling Difficulties: Drilling holes in loose, fragmented rock is challenging and time-consuming, often resulting in incomplete or collapsed boreholes.
- Grouting Challenges: Ensuring full and effective grouting is difficult, particularly in highly fractured rock masses. Inadequate grouting can lead to voids and channels that allow water ingress and reduce the effectiveness of the support system.
- Durability Concerns: Traditional anchor bolts are prone to corrosion, especially in wet conditions, leading to reduced durability and the need for frequent maintenance or replacement.
Advantages of Self-Drilling Hollow Anchor Bars
Self-drilling hollow anchor bars offer a solution to the limitations of traditional support methods, providing several key advantages: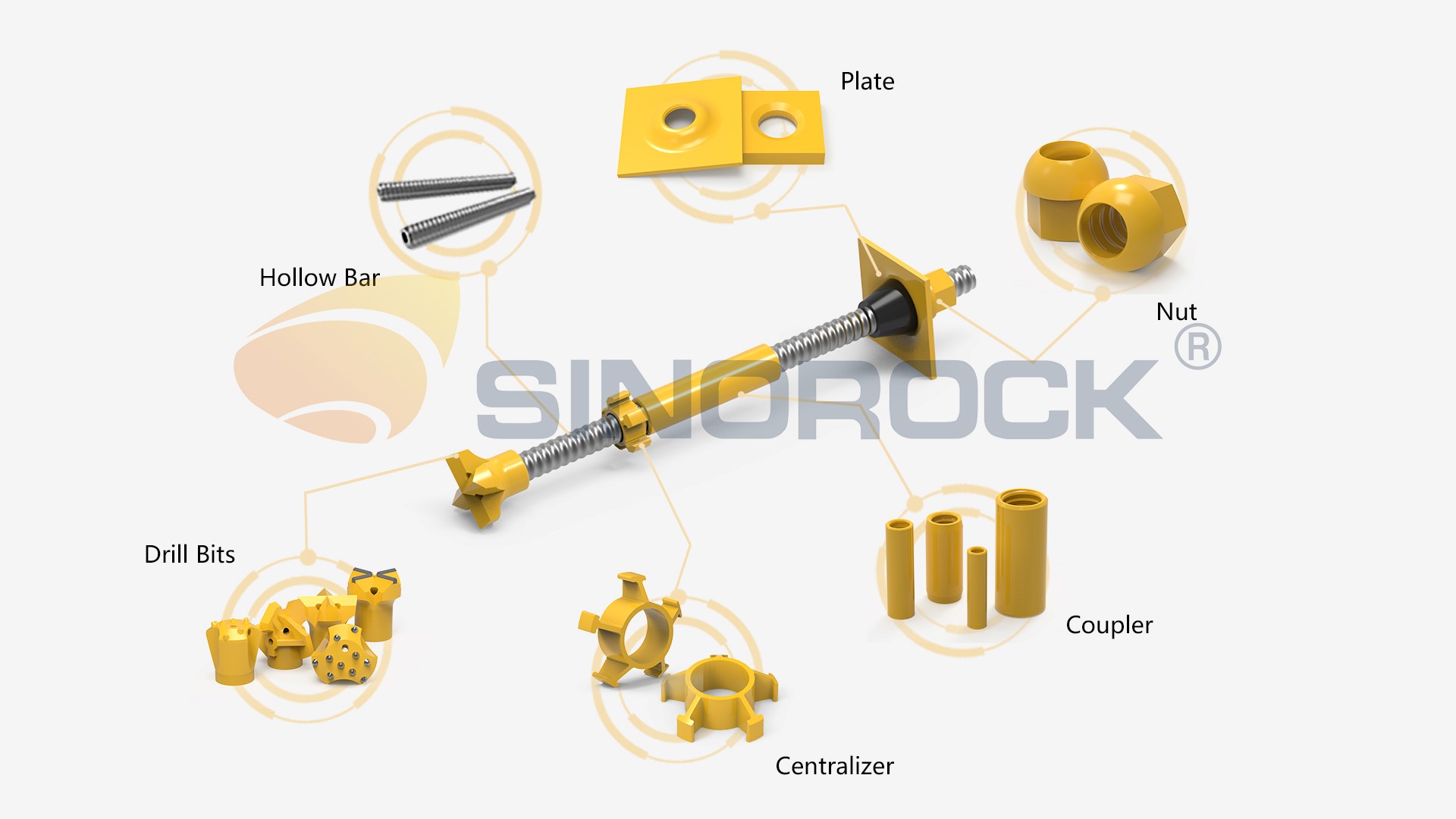
Integrated Drilling and Grouting
One of the primary benefits of self-drilling hollow anchor bars is their ability to combine drilling and grouting into a single operation. This integrated approach offers several advantages:
- Efficiency: The self-drilling capability allows for rapid installation, reducing the time required for drilling and grouting operations.
- Improved Grouting: The hollow core of the anchor bar allows for continuous grouting during installation, ensuring full encapsulation of the anchor and effective penetration of the grout into the surrounding rock mass.
Enhanced Stability and Integrity
The grouting process not only fills voids and fractures within the rock mass but also improves the overall stability and integrity of the surrounding rocks. This enhanced stability is achieved through:
- Air and Moisture Ejection: The pressure of the grouting process forces air and moisture out of the rock mass, helping to solidify loose materials and improve cohesion.
- Bonding and Reinforcement: The grout acts as a binding agent, connecting the anchor bar to the surrounding rocks and enhancing the overall strength and stability of the tunnel.
Durability and Corrosion Resistance
Self-drilling hollow anchor bars are designed to resist corrosion and provide long-lasting support in challenging conditions. This durability is achieved through:
- High-Quality Materials: The anchor bars are typically made from high-strength steel that is treated to resist corrosion.
- Protective Coatings: Additional protective coatings can be applied to further enhance the corrosion resistance of the anchor bars.
Working Principles of Self-Drilling Hollow Anchor Bars
Drilling
The self-drilling hollow anchor bar is equipped with a sacrificial drill bit at its tip, which allows it to penetrate through loose and fragmented rock efficiently. The drilling process involves:- Percussive Drilling: The anchor bar is driven into the rock using a combination of rotary and percussive forces, which helps to break up the rock and create a stable borehole.
- Continuous Penetration: The hollow design of the anchor bar allows for continuous penetration, reducing the risk of borehole collapse and ensuring a stable path for grouting.
Grouting
Once the anchor bar has reached the desired depth, the grouting process begins. This involves:
- Non-Choking Grout Flow: The hollow core of the anchor bar allows for a continuous flow of grout, which helps to ensure complete encapsulation of the anchor and effective penetration into the surrounding rock mass.
- Pressure Grouting: The grout is injected under pressure, which helps to force it into voids and fractures within the rock mass, improving the overall stability and integrity of the surrounding rocks.
Anchoring
The final stage of the process involves anchoring the self-drilling hollow anchor bar in place. This is achieved through:
- Grout Hardening: The injected grout hardens over time, creating a solid bond between the anchor bar and the surrounding rocks.
- Load Transfer: The hardened grout transfers the load from the surrounding rocks to the anchor bar, providing effective support and stability for the tunnel.
Case Studies
Case Study 1: Tunnel Construction in Water-Rich Conditions
In a tunnel construction project located in a water-rich area with IV-V class surrounding rocks, traditional support methods proved ineffective due to the high water inflow and instability of the rock mass. The introduction of self-drilling hollow anchor bars provided a solution to these challenges:
- Improved Stability: The pressure grouting process helped to eject air and moisture from the rock mass, improving overall stability and reducing the risk of collapse.
- Enhanced Durability: The corrosion-resistant design of the anchor bars ensured long-lasting support, even in wet conditions.
Case Study 2: Slope Stabilization in Loose Rock
In a slope stabilization project involving loose, fragmented rock, self-drilling hollow anchor bars were used to provide effective support:
- Rapid Installation: The self-drilling capability allowed for rapid installation, reducing the overall time and cost of the project.
- Effective Grouting: The continuous grouting process ensured full encapsulation of the anchor bars and improved the overall stability of the slope.
Conclusion
The application of self-drilling hollow anchor bars in IV-V class surrounding rock tunnels offers a significant advancement over traditional support methods. By combining drilling, grouting, and anchoring into a single operation, these anchor bars provide efficient, reliable, and durable support for complex geological conditions. As demonstrated in real-world applications, self-drilling hollow anchor bars can improve the stability and integrity of tunnels, reduce construction time and costs, and enhance overall safety. As the tunneling industry continues to evolve, the adoption of innovative solutions like self-drilling hollow anchor bars will play a crucial role in addressing the challenges of modern tunnel construction.
latest news
-
- 3 Crucial Factors That Impact the Quality of Self-Drilling Hollow Bolts
- Time:2025-01-26From:This Site
- As we all know, the quality of the self-drilling hollow bolts is vital to the whole project. It determines if the project is safe for the people in future use. Then, what will affect the quality of the self-drilling hollow bolts?
- View details
-
- Self-Drilling Anchor Bolt Construction in Complex Geological Slope
- Time:2025-01-24From:This Site
- During construction, Self-drilling hollow anchor bolt integrates drilling, grouting and anchoring functions, which significantly improves drilling efficiency. And under the action of pressure pump, the grouting in the rock strata and voids is full, which ensures the grouting thickness and anchoring effect.
- View details
-
- How Does Self-drilling Rock Bolt Drill in Quicksand Geological Condition?
- Time:2025-01-19From:This Site
- This in-depth guide explores how self-drilling rock bolts function in quicksand geological conditions, covering the challenges, construction methods, and best practices for ensuring effective anchorage in unstable, fluidic soil layers.
- View details
-
- Quality Control: the Vital Factor of A SDA Bolt Factory
- Time:2025-01-09From:This Site
- Sinorock’s comprehensive quality control system, from supplier management to outgoing inspections, ensuring the highest standards for self-drilling anchor bolts in construction.
- View details
-
- International Women's Day with Strawberry-picking
- Time:2024-03-09From:This Site
- Marked the annual observance of International Women's Day, and to commemorate this significant event, Sinorock organized a special strawberry-picking event exclusively for its female employees.
- View details
-
- Celebrate the 74th anniversary of the founding of the People's Republic of China
- Time:2023-10-01From:This Site
- On October 1st every year, we observe the annual National Day, commemorating the birth of our beloved motherland.
- View details
-
- SINOROCK to Attend EXPOMINA PERÚ 2024 in Lima, Peru
- Time:2024-08-10From:This Site
- Sinorock to Attend EXPOMINA PERÚ 2024 in Lima, Peru
- View details
-
- SINOROCK to Participate in MINING AND METALS CENTRAL ASIA 2024
- Time:2024-08-08From:This Site
- SINOROCK to Participate in MINING AND METALS CENTRAL ASIA 2024
- View details
-
- SINOROCK Gears Up for UGOL ROSSII & MINING 2024 with Custom Mining Solutions
- Time:2024-05-15From:This Site
- SINOROCK is thrilled to announce its participation in the highly anticipated 32nd International Trade Fair for Mining Technology, UGOL ROSSII & MINING 2024. The event will take place at the Exhibition complex "Kuzbass Fair" in Novokuznetsk, Kemerovo region - Kuzbass, Russia, from June 4th to 7th, 2024.
- View details